Diamond Grinding vs. Micromilling
By Tom Kuennen, Contributing Editor
Diamond grinding of Portland cement concrete pavements and micromilling of bituminous asphalt pavements are superficially similar in concept, but that’s just about the only thing they have in common.
Diamond grinding of aging Portland cement concrete (PCC) pavements renews the pavement’s skid-resistance, and provides a smoother-riding pavement. And the resulting smoother profile reduces dynamic loading on the pavement, thus extending its service life.
On the other hand, micromilling, or fine-tooth milling – using conventional cold mills with fine-tooth drums and hardened teeth – can remove imperfections from an asphalt surface and prepare it for a super-smooth thin asphalt overlay in a manner superior to conventional cold milling. In some cases, it can even be used instead of grooving or grinding pavements.
Following several years of research, promotion has begun for a new permutation of the diamond grinding process, the Next Generation Concrete Surface (NGCS). As promoted by the International Grooving and Grinding Association (IGGA), the NGCS is said to suppress noise from concrete pavements while enhancing friction and smoothness. The NGCS is being promoted following three years of research at the Minnesota Road Research Project (MnROAD), the world’s largest and most comprehensive outdoor pavement laboratory.
Early in 2011, new NGCS test sections were constructed at the Virginia Tech Transportation Institute’s Smart Road test facility near Blacksburg, Va. In January, three test strips situated on two test areas were constructed, including a conventionally-diamond-ground section, and an area that was conventional followed by longitudinal grooving of each half of the lane using two different groove spacings, of 0.5 and 0.75 inches respectively.
Each of the two test areas were ground one-lane wide and 528 feet long, and will allow the institute to study the impact of grinding and grooving on profiler measurements and on friction test results. In addition, the sections allow the future evaluation of splash and spray, as the Virginia Tech facility has this capability as well.
Diamond Grinding PCC Pavements
Diamond grinding is a concrete pavement preservation technique that corrects a variety of surface imperfections on concrete pavements, and should be used in conjunction with other pavement preservation techniques, reports IGGA.
It involves the removal of a thin layer of the cured concrete surface using a dedicated, self-propelled machine with closely-spaced diamond-coated circular saw blades. Diamond grinding restores rideability by removing surface irregularities. The immediate effect of diamond grinding is a significant improvement in the smoothness of a pavement, and a significant increase in surface macrotexture with improvement in skid resistance, noise reduction and safety.
The value of diamond grinding is borne out by a California Department of Transportation (Caltrans) study, conducted to quantify the expected longevity of a diamond-ground PCC pavement, and its overall effectiveness under various weather conditions and construction practices. In the study, Caltrans reported that diamond grinding “is a viable and cost-effective rehabilitation measure when properly applied. Diamond grinding not only extends the service life of a concrete pavement, but it also reduces tire-pavement interface noise and improves texture and skid resistance. Because the pavement is much smoother after grinding, highway user costs are also reduced through improved fuel efficiency and lower vehicle maintenance costs.”
Diamond grinding provides a smooth surface that can reduce dynamic loading and increase pavement longevity, IGGA reports. Increased pavement life will be obtained by reducing the roughness, IGGA maintains, and can be demonstrated using the American Association of State Highway & Transportation Officials (AASHTO) 1993 Pavement Design Equation. In that equation, serviceability is analogous to smoothness, which means that increased serviceability (a smoother pavement) will result in more equivalent single-axle loads carried by the pavement, the association says.
Diamond-ground surfaces have been found to reduce accident rates, IGGA reports. The Wisconsin DOT, working with Marquette University, found that the overall accident rate for diamond-ground surfaces was only 60 percent of the rate for nonground surfaces. The diamond-ground pavements provided significantly-reduced accident rates up to six years after grinding.
While creating a smoother pavement, diamond grinding does not affect the fatigue life of a pavement and does not raise the pavement surface elevation. Grinding also does not affect the hydraulic capacities of curbs and gutters on municipal streets, unlike bituminous overlays that fill curb and gutter, and reduce their drainage capabilities, IGGA says. Diamond grinding can be applied only where improvement is needed, and can be performed during off-peak hours.
Micromilling Asphalt Pavements
Unlike diamond grinding, micromilling pavements do not require a dedicated machine, as they can be applied by a conventional asphalt cold mill fitted with a fine-tooth drum.
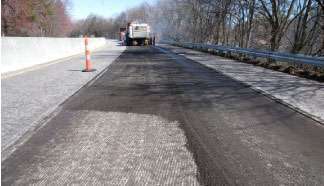
Micromilling, or fine milling, by Pavement Products and Services, provides super-smooth base for overlay while correcting cross-slope problems on I-185 in Greenville, S.C.
This is particularly important when placing so-called thin HMA overlays, microsurfacing or other spray surface treatments. There, micromilling is preferred to a conventional drum because the latter provides a “peaks-and-valleys” pattern that will be relatively high and deep. If an agency is not placing a lift that’s thicker than 1 to 1-1/4 inches, the rough surface can reflect through to the paved surface. But with 5/16-inch bit spacing (or less) – the definition of a fine-toothed drum – an owner or contractor can minimize the potential reflection of the peaks and valleys through the thin lift surface.
Georgia DOT’s micromill spec – Section 432: Mill Asphaltic Concrete Pavement (Micro-Mill) – describes micromilling of existing asphalt concrete pavement to remove wheel ruts and other surface irregularities, and restore proper grade and/or transverse slope of pavement as indicated in the plans or as instructed by the engineer.
“The planed surface shall provide a texture suitable for use as a temporary riding surface or an immediate overlay with OGFC [open-graded friction course] or PEM [porous European mix] with no further treatment or overlays,” Georgia DOT says in its spec, and limits use of the micromilled pavement as a temporary riding surface to a maximum of seven days.
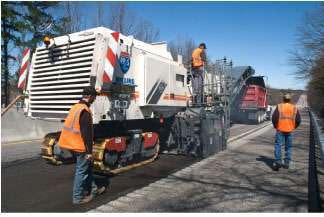
Control systems and a full lane-width, fine-mill drum allows Pavement Products and Services to correct pavement cross-slope using micromilling on I-185.
• equipped with a cutting mandrel [drum] with carbide-tipped cutting teeth designed for micromilling bituminous pavement to close tolerances;
• equipped with grade and slope controls operating from a stringline or ski and based on mechanical or sonic operation;
• capable of removing pavement to an accuracy of 1/16 inch (1.6 mm);
• furnished with a lighting system for night work, as necessary; and
• provided with conveyors capable of side, rear, or front loading to transfer the milled material from the roadway to a truck.
Prior to commencement of the work, Georgia DOT requires a 1,000-foot test section with uniformly-textured surface and cross section as approved by the engineer.
Next Generation Concrete Surface
While concrete diamond grinding has been limited to smoothing rough concrete surfaces, the Next Generation Concrete Surface offers a new application for enhancement of PCC pavement smoothness, friction and, especially, noise created at the tire-pavement interface. That’s important, because noise is more and more considered an emission into the environment that must be controlled.
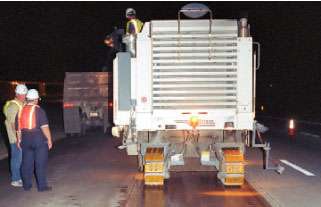
TexOp Construction uses a fine-toothed drum to prep President George Bush Turnpike near DFW Airport in advance of NovaChip overlay; the contractor alternative provided significant savings over diamond grinding originally planned by owner North Texas Tollway Authority.
The NGCS is a diamond saw-cut surface, designed to provide a consistent profile absent of positive or upward texture, resulting in a uniform land profile design with a predominantly negative texture. NGCS is a hybrid texture that resembles a combination of diamond grinding and longitudinal grooving.
The texture is most easily constructed in a two-pass operation using diamond-tipped saw blades mounted on conventional diamond grinding and grooving equipment. Testing has shown that these textures can be used for both new construction and rehabilitation of existing surfaces.
The construction method has two separate operations, reports the Washington State DOT in its April 2011 report, Evaluation of Long-Term Pavement Performance and Noise Characteristics of the Next Generation Concrete Surface. The first operation creates a flush ground surface and eliminates the joint or crack faults while providing lateral drainage by maintaining a constant cross slope between grinding extremities in each lane.
The second operation provides the longitudinal grooves, Washington DOT reports. The longitudinal grooves are 0.125 inches wide and 0.125 to 0.375 inches deep. The longitudinal grooves are spaced approximately 0.5 inches center to center. The grooves are constructed parallel to the centerline.
Patch-and-Grind Option
Another variation of diamond grooving and grinding is “patch-and-grind.” Cook County, Ill., in the heart of the Chicago metro area, reports great success serving its road users by using the patch-and-grind method of concrete pavement restoration.
Patch-and-grind involves full- or partial-depth concrete pavement patching and joint repair, followed by diamond grinding of the entire pavement. The patching addresses structural issues such as cracked panels and spalled joints, while the diamond grinding addresses the functional deficiencies.
Patching without diamond grinding can result in poor rideability and is not an attractive alternative when considering the most effective use of the taxpayer’s money, IGGA reports. But the patch-and-grind repair method has proven to be a lower-cost construction alternative when compared to a full reconstruction, the association says. Motorists also realize the benefit of the shorter construction duration.
The Cook County Highway Department has used diamond grinding on a growing number of projects and the technique has migrated into adjoining Lake County, Ill. Full reconstruction of these pavements would have cost the taxpayers three times more than the patch-and-grind technique, IGGA says. A full reconstruction costs approximately $45 to $50 per square yard, while a patch and grind costs approximately $15 a square yard.
“When a typical full reconstruction of a lane-mile costs $1 million, the use of patching and grinding makes sense because it can be done at a fraction of the cost, provides long-lasting repairs and creates far less inconvenience to the motoring public,” says John Beissel, P.E., assistant superintendent, Cook County Highway Department.
Micromilling Fixes Cross Slopes
Micromilling with cold mills isn’t limited to preparing asphalt pavements for thin asphalt overlays. South Carolina is taking a leadership position on micromilling to correct cross slopes, and it shows in the increase of fine milling jobs undertaken by one contractor, Pavement Products and Services (PPS), Piedmont, S.C.
“South Carolina has a lot of ‘flat’ roads,” says Douglas E. Limbaugh, the company’s project manager. “The cross slopes are out of balance. So, we will surface-plane or micromill an inch or two off the road, to get the aged asphalt off, and once that’s done, variable surface-plane or cross-slope correct the main lines or roadways.”
By doing the planing in two stages, the company eliminates the drop-offs that would result in doing the work in one pass. “Motorists don’t have to drive with more than a 1-inch drop, and in the meantime they get a better surface to drive on,” Limbaugh says.
In 2010, PPS was cold-milling day and night with fine-tooth drums. For example, in March 2010, during the day, the company was micromilling the I-185 expressway just southwest of downtown Greenville, S.C., and at night, was using some of the same equipment to micromill I-85 west of the city.
“Using our fine-tooth drums, we are removing an inch from I-185, then coming back the same day and fine-milling a second inch,” Limbaugh says. “We then will go to isolated areas and cross-slope correct there.” That project represented two 50,000-square-yard lifts, 100,000 total.
The I-85 work – three lanes both north and south – that night was part of a total 1.4 million square yards of 1-inch micromilling, and 295,000 square yards of variable surface planing for cross-slope correction. “We will be using two full-lane cold mills with 12.5-foot drums, and a half-lane micromill.”
The South Carolina DOT uses the terms “surface planing” but the same term applies to “fine milling” and “micromilling,” Limbaugh says. “The spacing on the cutter drum must be 0.2 inches, which translates to 5 mm spacing,” he said. “It means from chevron to chevron, or tooth mark to tooth mark, you have to have 5 mm or less.
“The state also requires tolerances of 1/8 inch from high to low on the tooth marks, so you can’t just put a thousand-tooth drum out there and run 80 feet per minute,” Limbaugh says. “You have to go at a steady pace, because that will leave as smooth a surface as you can. In ride quality, it’s comparable to a porous friction course.” On top of that, for cross-slope correction, the state imposes a rideability spec.
As standard bids are cut to the bone, these contractors strive to earn smoothness bonuses, which PPS makes easier by its fine milling. “We are setting them up not to fail, but to win, by giving them a superior surface,” Limbaugh says.
Fine-Mill Grooving Substitute?
Micromilling with a fine-tooth drum also can be used on driving surfaces just to restore friction and smoothness.
For example, fine milling or texturing may be appropriate for a county that does not have a lot of money to mill out and pave its roads completely, and they may just want to shape up the roads and remove some rutting and areas where asphalt is shoved in intersections. “A fine milling drum can be put in a cold mill and used to repair that driving surface,” says Jeff Wiley, senior vice president with equipment manufacturer Wirtgen America. “The county will have bought some time while being able to open a road to traffic immediately.”
With a narrower drum on a smaller cold mill, fine milling is also useful for removal of road markings, or for prepping pavements for road-marking application.
But in limited instances – at least when a pavement is prepped for an overlay – micromilling with a fine-tooth drum can replace diamond grinding of existing pavement. For example, not too long ago, micromilling was used instead of the specified diamond grinding of the driving surface of the President George Bush Turnpike north of Dallas.
There, the President George Bush Turnpike is a major east-west route in the northern half of the Dallas Metroplex, and is a 30.5-mile, six-lane, limited-access toll highway that passes through or along the cities of Garland, Richardson, Plano, Dallas, Carrollton, Farmers Branch and Irving.
The turnpike owner – the North Texas Tollway Authority – planned to overlay a section of the expressway with NovaChip proprietary open-graded friction course. But such thin lifts – with maximum 3/8-inch stone – require extremely well-prepared and even surfaces for placement. Any irregularity in the existing pavement will reflect through the thin surfacing immediately.
Conventional surface prep for worn pavements previously involved diamond grinding the pavement to precise tolerances. But cold milling subcontractor TexOp Construction, Roanoke, Tex., in conjunction with its general contractor APAC, proposed to cold-mill using a 2-meter (6.56-foot) fine-tooth drum to prepare and level the aged asphalt pavement surface prior to the thin surfacing.
The project already had been designed with diamond grinding in the contract, so a change order was the means to get the cold mill on the project instead of a diamond grinder. On this particular job, fine-texturing with a cold mill saved the authority a significant sum over diamond grinding. Also, the diamond grinders were asking for a minimum 60 days, and the contractor was on track to finish the same area in 10 to 14 days.
“There was a very high cost to the diamond grinding,” says Danny Simpson, vice president and managing partner, TexOp Construction. “Also, the time it would take to do the diamond grinding was excessively long. We proposed to do the job in a much shorter period of time at a lower cost, but with the same benefit as the diamond grinding, 20 days versus 60 days, giving them exactly the same ride in a third of the time.”
First, both the turnpike authority and the Texas DOT requested a test section. “We did a test project for Texas DOT using the fine-texture drum,” Simpson says. “People came out, took a look and liked what they saw, including the smoothness of the ride and the pattern of the drum. They were skeptical until they saw the process work.”