One and One is One
Two lifts can become a single, strong layer.
By Tom Kuennen, Contributing Editor
With two-lift hot mix asphalt paving, it’s a case of 1+1=1.
As more durable hot mix asphalt pavement designs are explored in the United States, two-lift asphalt paving as it’s practiced in Europe offers potential for consideration.
At the same time, two-lift concrete paving also is winning converts.
Two-lift HMA paving describes the placement and compaction at-screed of an intermediate lift of asphalt, followed immediately by placement and compaction at-screed of the friction or surface course. Placement of two layers of hot mix asphalt – hot-on-hot, so to speak – provides a durable, near-monolithic layer of asphalt that resists traffic loads and pavement ills.
Instead of subsequent placement of a hot, flat friction course on top of a cold, flat intermediate layer – with only a messy tack coat to bond them – true hot-on-hot bonding, with aggregate interlock, is provided with the varieties of two-lift HMA paving.
The downside is the added cost. And for the contractor, placement can be complicated, with the use of a material transfer vehicle and one or two modified asphalt pavers with high-compaction screeds, according to its two current permutations from European manufacturers. Staging of multiple trucks with two different mixes, from two different plants, is the norm.
And while two-lift hot mix asphalt paving is uncommon, even in Europe where it is being popularized, on these shores it’s still worth a look because it may become part of our “toolbox” of asphalt paving techniques in the years to come.
That’s why Eurostyle two-lift asphalt paving was described as a “paving technique of the future” by National Asphalt Pavement Association Vice President-Research and Technology Dave Newcomb, P.E., Ph.D., at a workshop on asphalt paving for trade journal editors at the National Center for Asphalt Technology at Auburn University a few years ago.
Also, consider that two-lift paving already exists in other forms in the United States. For example, hot-in-place recycling as implemented by one recycling contractor recycles and rejuvenates the existing asphalt surface into an intermediate course, and on it immediately places a surface course of virgin hot mix asphalt. The result of this hot-on-hot technique is a near-monolithic pavement with aggregate interlock, but utilizing an intermediate layer of 100 percent recycled asphalt pavement (RAP).
Further, NovaChip surface treatment and its generic clones simultaneously spray hot polymer modified binder on swept pavement immediately ahead of a hot, open-graded asphalt mix, with immediate placement of a polymer modified open-graded mix, or immediate placement of aggregate, followed by an immediate second spray of polymer or rubber modified binder. Either way, the result is a durable, open-graded, thin surfacing that stands up to Interstate-level traffic.
For the portland cement concrete side, two-lift “wet-on-wet” PCC pavements already are actively promoted in the United States, with a number of demonstration placements each year.
Here’s a look at the status of two-lift HMA paving today:
InLine Pave from Vögele
A two-lift HMA placement technique that has achieved some degree of success in Europe, but no penetration in the United States, is the InLine Pave process from Joseph Vögele AG.
“InLine Pave is a cutting-edge process,” says Brodie Hutchins, general manager, Vögele America, Inc., Chambersburg, Pa. “It has not swept the world or Europe or Germany. But Vögele has sold several trains to European contractors, and some specifying agencies are studying the process, to fully understand the advantages.”
The InLine Pave process involves the placement of two layers of pavement at the same time, a hot-on-hot process, Hutchins told Better Roads. “The paving train starts with a material transfer vehicle or material feeder that puts a binder mix into the first paver, and a wearing course into the paver right behind the first,” he said.
As with Dynapac’s Compactasphalt process (below), two separate mixes must be fed into a single laydown machine or train.
“It becomes a logistical challenge for the plant,” Hutchins said. “Some truckers will be picking up a 9mm or 11mm mix for the surface course, while others will be picking up a 25mm mix for the binder course. They have to communicate with the material transfer vehicle operator so he will know into which machine to place the mix, either directly into the hopper insert of the binder course paver, or the conveyor which supplies the surface course to the end paver.”
This also necessitates two plants making two different mix designs. “Two different mixes will be ‘cooked’ at the same time,” Hutchins said.
The InLine paving process also requires a great deal of compaction at the screeds of the pavers. “Both pavers with have high-compaction devices,” Hutchins told Better Roads. “These will be tamping screeds, and the first paver – the middle machine in the train – will be placing HMA with a pressure bar screed. Typically for InLine, this will involve a Super 2100-2 paver with TP-2 screed that is putting down a thicker layer of binder. Behind that, most contractors will use a somewhat smaller machine like a Super 1600-2, as it’s putting down a thinner surface course, and these machines will have a single tamping screed that can lay a mat fairly wide.”
For the U.S. paving community that typically favors relatively high-speed placement of HMA pavements, slower two-lift HMA paving is a hard sell. “Two-lift paving is an elaborate set-up, with a lot to orchestrate, in our case three machines and two different plants,” Hutchins said. “Most of the type of work going on here – milling and resurfacing – does not justify a process this elaborate. But it holds potential for placing high-performance perpetual pavements on new alignment.”
Compactasphalt from Dynapac
Contemporaneous with Vögele’s InLine Pave is Dynapac’s Compactasphalt process. This two-lift process uses a single, large paver, modified with two hoppers and two screeds. It has the advantage of using just one paver, along with a material transfer vehicle.
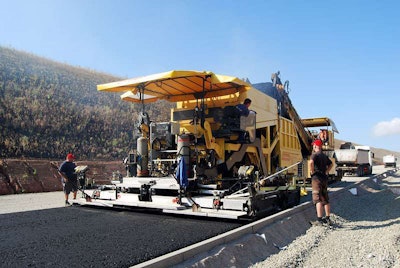
“The Compactasphalt technology is the one and only technology officially approved in the German regulation for road construction ZTV-Asphalt-StB07 as a regular paving method,” says Roland Egervari, product manager for Compactasphalt. “The regulation forbids that a second vehicle [paver] runs on the hot binder layer.”
Dynapac has improved its two-lift system and has released a new plant, the CM2500 Compactasphalt modular system. It features enlarged hoppers and a unique drive system, the firm says.
Designed to be used with Dynapac’s DF145CS paver, the CM2500 module’s 8.37-foot width is ideal for applying the Compactasphalt method on highways up to 24-foot wide, the firm says. The Compactasphalt 2500 features an enlarged hopper for binder material with a total capacity of 28 tons. Equipped with its own power unit, the module also has a 15-ton hopper for the top layer material.
This hopper features two augers, which allow the top layer material to be carried under the electrically-heated VB5100TV-E screed. A second screed, Dynapac’s VB805TV Plus-E high compaction screed, compacts the binder layer. Both screeds are synchronized in the case of slope and cross-slope changes.
The support frame is a minimally-modified serial paver that is predominantly used for standard construction methods, and which can be converted into a modular paver, when necessary, at low cost. This guarantees a high degree of utilization.
The use of a modular paver allows for the use of paving-improving additives or low-viscosity asphalts in the binder area. Only one crew is needed to operate the modular paver.
With the Compactasphalt process, both paving screeds are coupled in succession to the frame of the modular paver. This meets the identically-defined conditions whereby it is possible to achieve a consistent thickness of the upper layer, independent of the load-bearing performance of the hot base, Dynapac says.
While significantly different from the Vögele process, the Compactasphalt 2500 – like Vögele’s InLine Pave – simultaneously places both the wearing and binder courses – hot-on-hot – in a single pass. The result is a better interlocking of the courses that increases the durability of the layers. Furthermore, the residual heat of the hot binder course significantly increases the time available for final compaction.
Dynapac says its system means only one paver crew is needed to place two asphalt layers. The Dynapac DF145CS paver can be quickly configured for both conventional and Compactasphalt paving, and can be transported on a low-bed trailer with the CM2500 modular system in place.
Evaluation at NCAT Track
The Compactasphalt system has come a little closer to home, as it was used to place a test section at NCAT’s Test Track near Auburn, Ala., which Dynapac says was the first instance of this style of two-lift, hot-on-hot HMA paving – without a tack coat – in this country.
Using an earlier model of the Compactasphalt system, based on Dynapac’s F 300 CR two-lift paver, the paver placed an open-graded porous asphalt lift, two-layered, in thicknesses of 35mm and 20mm, with particle diameters of 12.5mm and 9.5mm, respectively, for the Georgia DOT at NCAT’s Test Track.
The test section was designed to place two courses of pavement simultaneously for a distance of 200-feet. in length and 17-feet 7-inches in width, Dynapac says. There was an additional special start up section 25-feet long by 18-feet 4-inches wide devised prior to the actual test section, needed in order to establish the desired thickness of the actual test section.
After all test sections (including the Compactasphalt) were placed, the field testing started in September 2006, in the course of which a traffic load produced in 18 years would be simulated within two years. To this end, trucks pulling three trailers loaded with steel plates drove over the testing area daily.
After 24 months of applying constant loads, the void contents and the initial evenness in this field were just the same as on the first day, Dynapac says. “Two additional fields were paved during the application process, using the same materials and a “hot-on-cold“ method, but their results were less promising,” the firm says.
Hot-on-Hot Repaving
While there are a number of varieties of hot in-place (HIR) recycling, one elevates the technique by the placement of a lift of virgin HMA immediately on top of the hot-recycled intermediate course.
With this recycling train technique, as implemented by Cutler Repaving, Inc., Lawrence, Kan., the existing pavement is heated to 300 degrees F. When in a resulting softened, pliant condition, the pavement is scarified to a depth of 1 inch., and while in the mobile repaving unit, a recycling agent that restores the viscosity of the aged asphalt is mixed into the scarified, reclaimed asphalt.
This reclaimed material then is distributed with a screed as a 1-inch leveling course. While that material remains at a minimum 225 degrees F, a virgin hot mix asphalt overlay is placed over the recycled leveling course.
Thus, Cutler’s repaving machine scarifies applies recycling agent, places the leveling course, and applies the new overlay simultaneously in one pass. That benefits road users because there is no delay between the time the pavement is recycled and the time a riding or friction course is placed, resulting in a safer work zone for road users and for contractor personnel. Also, no tack coat is required, eliminating concomitant problems of tracking onto pavement, into parking lots, and even into stores and offices.
Because the hot virgin mix is placed over the heated, recycled leveling course, the process achieves a thermal bond between the recycled layer and the new layer, with aggregate interlock between the layers.
“From an engineering point of view, there is no delamination between the recycled layer and the new overlay,” says Cutler vice president John Rathbun. “No tack coat is required because the heat is the bonding factor. The heat locks those two layers and aggregates together. A bond is achieved between the hot liquid asphalt of both layers, and between the aggregates of the virgin material interlocking with the aggregates of the recycled material.”
Hot-on-Hot Surface Treatments
High-performance surface treatments like NovaChip and its “clones” are another example of hot-on-hot paving. NovaChip is marketed as a pavement rehabilitation, preventive maintenance or surface treatment that has a durable surface with improved skid, wear, and rutting resistance, reports the Washington State DOT.
NovaChip was developed in France by the construction firm Screg Routes in 1986. The system utilizes a single piece of equipment to place a thin, gap-graded hot mix asphalt (HMA) onto a relatively thick membrane or layer of polymer modified asphalt emulsion tack coat.
“NovaChip is a paving process that places a thin gap-graded (3/4- to 3/8-inch) mix over a liquid membrane – a polymer modified emulsion that is specially designed to seal the existing roadway and provide a strong bond with the NovaChip asphalt material,” the DOT says.
Similar to conventional HMA, NovaChip is easily produced at a HMA facility and placed with little difficulty, according to DOT. The main difference in the placement of NovaChip verses typical HMA is the use of a specialized paver, which allows the placement of the initial polymer modified “membrane” and NovaChip surfacing in a single pass.
The purpose of compaction during NovaChip placement is to seat the asphalt into the membrane rather than to obtain density. Compaction is partially obtained by vibration at the screed of the paver, and then by one or two passes from double-drum rollers operating in the static mode.
Pavers appropriate for NovaChip are similar to those for hot mix paving, but with an emulsion tank added for the initial placement. Immediately following placement of the polymer emulsion membrane, the ultrathin gap-graded hot mix asphalt is applied, which can be placed as thin as 0.5 inches (12.5mm) to 1.5 inches (38mm) thick. The emulsion cools quickly and rapidly bonds the asphalt to the pavement rapidly. Following the static compaction, the new surface can be reopened to traffic within 300 feet of the train.
The open-graded mix is seated by a tamper bar on the modified paver, and further seated by a roller which follows the paver. As the membrane cures as its temperature drops, the roller must work within a window of temperature range. Typically, traffic can be allowed on the surface treatment in as little as 20 minutes after placement.
The surface texture of NovaChip is very similar to that of a typical open-graded friction course, with the benefits of reduced surface water spray from vehicles, improved friction, and attenuation of noise at the pavement/tire interface.
NovaChip surfaces have significantly higher pavement surface friction numbers compared to dense-graded HMA wearing course, NCAT reported in 1997. It is marketed as an alternate to conventional chip seals, micro-surfacing, and open-graded friction courses.
Variations of NovaChip
A variation of this process involves placement of hot binder, immediately followed by an open-graded surfacing. For example, California’s rubberized open-graded wearing course consists of an initial sprayed layer of polymerized binder, deposition of 3/8-inch aggregate, and an immediate spray of rubberized binder, all in one pass by a single machine, followed by finish rolling. The wearing course typically is placed 5/8 up to 7/8 inch thick, depending on Caltrans specs, and on Calif. 101, was being placed 12.5-feet wide – a full lane.
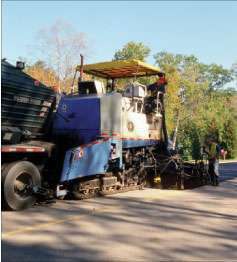
A paver modified for this process will have an integral spray system that sprays polymer modified binder in front of the mix being laid, followed immediately by aggregate, and then a second spray of rubberized binder. The advantage is less mess, with no traffic or construction equipment tracking the binder before the aggregate is placed.
The first binder, the polymerized emulsion, is placed at 175 degrees F, while the rubberized binder comes out between 295 to 325 degrees F. Once the aggregate hits the oil below, it breaks it, and wicks up binder through capillary action through the aggregate mix, giving it its binding power. The immediate, subsequent application of rubberized binder from the modified paver coats the entire structure, penetrates downward, and melds with the bottom lift of binder, which retains its heat, creating a “hot-on-hot” near-monolithic wearing course that will hold up to the Central Valley’s punishing traffic and heat waves.
NovaChip cures within five to 10 minutes, while the rubberized wearing course takes a little longer, depending on how thick the wearing course is placed. One such spray paver has a tamper bar which compacts the mix behind the screed to 95 percent, while still keeping its open-graded character. Sweeping and sometimes crack filling are the only preparation needed ahead of a rubberized open-graded wearing course.
Two-Lift Concrete
In addition to new techniques of bituminous two-lift paving, two-lift portland cement concrete has been placed in Europe and the United States. In fact, field examples of two-lift PCC construction are more numerous in the United States than conventional two-lift HMA paving.
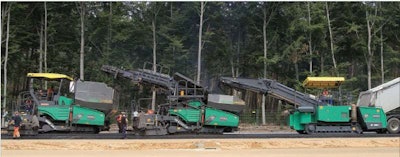
Used for decades for wire mesh placement in concrete pavements, two-lift paving was recommended for implementation in the United States following a May 2006 international scanning tour on long-life concrete pavements as part of the Federal Highway Administration’s (FHWA) Highways for LIFE program.
Two-lift concrete construction involves the placement of two wet-on-wet layers of concrete, or bonding of wet to dry layers of concrete, instead of the homogenous single lift most commonly placed in concrete paving.
With two-lift paving, a thick bottom layer contains aggregate of lesser quality, lower durability or strength, locally-available aggregate, or more often, recycled aggregate composed of recycled concrete or reclaimed asphalt. A thinner top layer consists of premium aggregate, perhaps non-locally sourced, designed to provide superior resistance to freeze-thaw damage as well as noise reduction and improved traction. Two-lift construction can also accommodate the use of an exposed aggregate surface to mitigate noise.
Balancing the environmental and skid-resistant benefits of two-lift paving are inescapable higher costs. Either two concrete pavers – or a combination paver which places two lifts at once – is required, along with two concrete plants nearby, plus added labor and trucking costs. However, the use of secondary materials such as reclaimed crushed concrete pavement or reclaimed asphalt pavement – perhaps sourced on the same project under construction – can undercut the added costs.
Austria, Belgium, the Netherlands, Germany, and the United Kingdom are all currently using two-lift paving. States currently looking into using two-lift paving include Iowa, Kansas, Florida and Washington. For more information, see our article Roadbuilders to Get Fresh Look at Two-Lift Concrete Paving, June 2008, pp 22-29.v
Two Hot Lifts Equal One Durable Pavement
Eurostyle technique not seen in U.S., but variations are