?%#
What percentage of RAP is best? It depends.
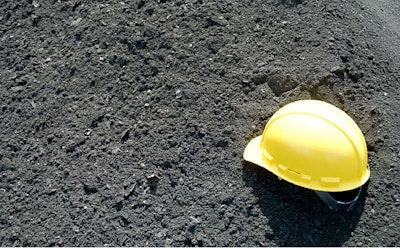
T here are powerful inducements today to reuse reclaimed asphalt pavement (RAP) in a variety of applications. And the big question about RAP has shifted from whether it belongs in mixes at all, to how much can safely be accommodated in a mix.
It is this question that is driving an enormous amount of attention and research today. Many road agencies are closely observing the research as they permit higher percentages of RAP in a mix. Environmental legislation at the state level also is compelling higher percentages of RAP.
In the meantime, research continues on the questions of to what degree does the residual asphalt on RAP replace performance-graded (PG) binders; how will larger percentages of RAP impact the type of PG binder that should be specified for a Superpave mix in a particular location; and how important is the processing and analysis of RAP stockpiles in allowing higher percentages of RAP in asphalt mixes.
New guidance was released this year and last from the Federal Highway Administration (FHWA) and the National Cooperative Highway Research Program (NCHRP) on higher amounts of RAP in asphalt mixes.
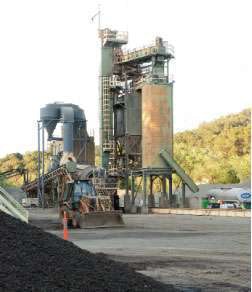
Today, critical-performance mixes – such as those for surface or friction courses – typically get a lower percentage of RAP allowed than the intermediate or leveling courses just below them. It’s being demonstrated that warm-mix asphalt (WMA) modifiers can permit higher percentages of RAP in a mix, and that warm mixes are very friendly to RAP. Use of a rejuvenator can allow vastly higher percentages of RAP in noncritical intermediate courses. And foamed asphalt- or asphalt emulsion-stabilized bases can use 100-percent RAP, as was done in a major recycling project on Interstate 81 in Virginia this year.
In 2009, researchers at the National Center for Asphalt Technology (NCAT) estimated that across the United States, RAP usage varied considerably, but the average RAP content was estimated to be around 15 percent. Boosting that average could reduce greenhouse gas emissions from roadbuilding substantially, National Asphalt Pavement Association (NAPA) president Mike Acott says. “Use of 25-percent RAP reduces total lifecycle greenhouse gas emissions by 10 percent, which equates to 2 million tons [of carbon dioxide] offset annually,” he says.
And more emissions reduction is possible, Acott implies: “A singular quality of asphalt cement in that it is rejuvenated when RAP is incorporated into new pavement, becoming an integral part of the binder. In view of the high reuse/recycling rate in lead states, including a preponderance of evidence that the quality of asphalt pavements incorporating RAP is equal to or better than pavements using all virgin materials, there is ample opportunity to double the quantity of RAP used within five years.”
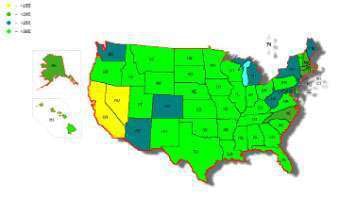
Boosting the amount of RAP in mixes is a line item in the National Asphalt Road Map: Commitment to the Future, produced in 2007 by NAPA; FHWA; American Association of State Highway & Transportation Officials; Asphalt Institute; and National Stone, Sand & Gravel Association.
The asphalt road map lists Item No. 4.09: Develop High RAP Content Mix Design Procedure as one of its needed high-priority research projects. The road map also urges study on use of recycled materials other than RAP in asphalt mixes.
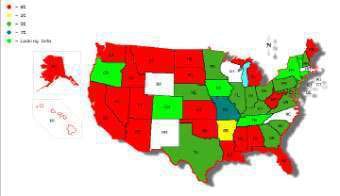
“The use of RAP in recycled asphalt pavement is well accepted practice by many federal, state and local agencies,” the road map says. “In many areas, almost all hot-mix asphalt (HMA) contains at least some RAP. However, with a few exceptions, the amount of RAP that can be added in hot plant mix asphalt mixtures is limited to relatively low percentages and in some areas the use of RAP is prohibited in certain types of mixtures, such as surface courses. Typically, the maximum percentage of RAP allowed is anywhere from 15 to 30 percent by weight of HMA mixture.”
The road map anticipates considerably higher percentages being implemented. “Laboratory and field studies have been performed on HMA with much higher percentages of RAP,” the road map says. “These investigations have concluded that HMA materials with percentages in excess of 50 percent can be produced to perform the same as ‘virgin’ mixes. It has been well established that agencies that are not currently allowing RAP into their HMA mixtures and those that are only allowing small percentages of RAP can safely increase the amount of RAP used without fear of shortening pavement life, provided that best practices are followed. . . . [T]he state-of-the-practice relative to the mix design procedures using high RAP content mixes needs to be established.”
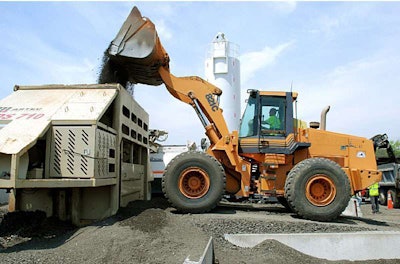
To this end, last year, the leaders of trade associations that represent 150 million tons a year of asphalt recycling signed a cooperative agreement aimed at doubling the rate of reuse/recycling of asphalt pavements within five years.
Principal signatories to the agreement were NAPA and the Asphalt Recycling & Reclaiming Association (ARRA). Letters of support were provided by the FHWA and EPA. Under the agreement, NAPA and ARRA pledge to support each other’s efforts to deal with common challenges and build on each other’s strengths regarding asphalt recycling issues.
“Asphalt pavement is America’s most recycled material,” says NAPA’s Acott. “There are more than 18 billion tons of asphalt pavement already in place on the roads, streets and highways of this country. These same roads that Americans use every day are also a resource that future generations can use. Our goal is to increase the rate of recycling even further.”
“Reclaiming and recycling asphalt roads brings America the best possible pavements while conserving precious natural resources,” says Mike Krissoff, executive director of ARRA. “The members of both ARRA and NAPA are proud of the industry’s long track record of delivering quality and value.”
Complications
Efforts to boost RAP usage are restrained by the fact that larger-than-conventional doses of RAP – without binder adaptation – can complicate long-term mix performance.
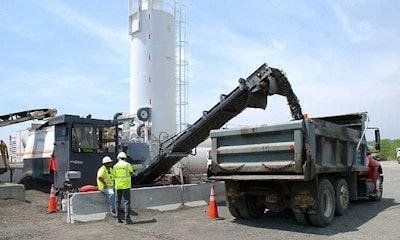
One “rap” against RAP is that its composition varies because it’s sourced from a wide variety of locations. Therefore, advance knowledge of the composition of the residual binder in RAP – along with the separate stockpiling of different varieties, or blending of varieties to create a consistent product – is necessary for creation of reliable mixes.
One way to boost use and consistency of RAP in asphalt mixes is for producers to maintain sheltered, blended RAP stockpiles and, if needed, to reprocess, or fractionate, the RAP into individual gradations. Sheltered stockpiles are favored because RAP doesn’t shed water as easily as virgin aggregate.
The processing, or “fractionation,” of RAP replicates conventional best practices for virgin aggregate processing. With fractionation, RAP is screened, with oversize broken into smaller fractions and each stockpiled separately. Fractionated RAP may result in more uniform mixes, in which RAP fractions can be isolated, in contrast to general stockpiles in which large and smaller fractions may become segregated.
Long ago it was established that RAP was not just a “black rock,” but that its residual asphalt – oxidized and brittle as it is, and in varying amounts – still provides a bituminous portion to the overall mix design, permitting addition of a lesser amount of expensive liquid asphalt binder. The Asphalt Institute (AI)stated components of RAP have value, particularly true of asphalt binder, and the residual asphalt can reduce the amount of new asphalt binder in a mixture. A mix with 20-percent RAP with 5-percent asphalt content can result in a 1-percent savings in new asphalt binder, AI says.
RAP = Stiffer Mixture
Excessive amounts of RAP in the mixture can have substantial effects on pavement performance. Use of 15-percent or more RAP can result in a significant increase in stiffness of the mixture, which can enhance durability. But the use of RAP in hot-mix asphalt also can negatively affect low temperature cracking characteristics of the pavement.
“The aggregate in RAP should be considered as if it were just another stockpile of virgin aggregate,” states the Washington State DOT in an online tutorial. “RAP aggregate properties, as with virgin aggregate properties, may limit the amount of RAP that can be used in a particular mixture.”
The residual binder in RAP must be taken into account when designing a mix, WashDOT says. “The effect of RAP asphalt binder must be considered when using RAP in Superpave mix design (or any mix design),” the tutorial states. “RAP asphalt binder will blend with virgin asphalt binder in most any mix design, and the resulting properties of this blended asphalt binder must be understood.”
The reason is that RAP asphalt binder already is significantly aged because of its previous field life, WashDOT says. “This aged binder is generally stiffer than virgin asphalt binder and thus will cause the resultant binder blend to become more viscous (stiffer),” the tutorial says. “This, in turn, will cause the HMA to be more viscous.”
Therefore, successful RAP mix designs incorporating RAP above 15 percent by weight should analyze the stiffness of the existing residual binder in the RAP, and compare it to the stiffness of the virgin liquid binder, along with the proportions of each in the final product.
In their 2010 Transportation Research Board paper, A Backcalculation Method to Determine “Effective” Asphalt Binder Properties of RAP Mixtures, Thomas Bennert, Ph.D., senior research engineer, Rutgers University’s Center for Advanced Infrastructure and Transportation (CAIT), and Raj Dongré, Ph.D., Dongré Laboratory Services, Fairfax, Va., observe that it’s important to understand the effect that RAP has on the final asphalt mixture performance.
“Current recommendations for the use of RAP in asphalt mixtures follow those developed under NCHRP Project 9-12, Incorporation of Reclaimed Asphalt Pavement in the Superpave System,” they write. These include: no change in binder selection necessary for RAP percentages less than 15 percent; select a virgin binder grade one grade softer than normal for RAP percentages between 15 and 25 percent; and follow recommendations from blending charts when RAP percentages are greater than 25 percent. The results were based on laboratory testing of asphalt mixtures containing approximately 5-percent asphalt binder and using non-fractioned RAP.
‘Tiered’ Approach to Higher RAP
Similarly, New Jersey has taken an incremental approach in raising allowable percentages of RAP in its mixes, with evaluation of the residual RAP binder required for doses higher than 15 percent.
In his 2010 presentation, Higher RAP Mixes in New Jersey: Changes in Mix Design and Production, CAIT’s Bennert describes the efforts that New Jersey DOT is undergoing to incorporate higher levels of RAP in mixes while maintaining pavement durability.
New Jersey DOT has established “tiers” describing increasing levels of RAP in mixes.
• Tier 1: 10- to 15-percent RAP. Asphalt binder grade for the mixture is selected for the environmental and traffic conditions the same as required for a mixture with all virgin materials. With RAP limited to 15 percent or less, it is not necessary to determine the properties of the RAP binder. No [PG] grade adjustment is made to compensate for the stiffness of the asphalt binder in the RAP.
• Tier 2: 16- to 25-percent RAP. The asphalt binder grade can also be selected using an appropriate blending chart if the supplier chooses to adjust the binder selection to compensate for the stiffness of the reclaimed asphalt binder. Extraction and recovery of RAP binder with binder testing is required. Regardless of the method used to select binder grade, adjust binder grade as necessary to meet mixture performance requirements
• Tier 3: 26- to 40-percent RAP. The binder grade for the new asphalt binder is selected using an appropriate blending chart for high and low temperatures. Extraction and recovery of RAP binder and testing is required on a minimum of five samples. Adjust binder grade as necessary to meet mixture performance requirements.
Indiana Justifies More RAP
Use of larger amounts of RAP – and thus changes in a state’s RAP acceptance spec – can be justified by adjusting the type of PG grading used for a Superpave mix, say Matthew Beeson and Michael Prather, Indiana DOT, and Gerry Huber, Heritage Research Group, in their 2011 TRB paper, Characterization of Reclaimed Asphalt Pavement in Indiana: Changing INDOT Specification for RAP.
But doing so requires intensive study of the binder properties in the existing storehouse of RAP across the state, and comparing them to the properties of new asphalt binders being used in the state.
“Interest has been growing to increase reclaimed asphalt pavement usage by increasing the allowable percentage that can be used in hot-mix asphalt,” Beeson, Prather and Huber say. “[Indiana DOT] undertook a detailed evaluation of asphalt binder properties in RAP and the properties of new asphalt binders being supplied to INDOT.”
Asphalt binder was recovered from 33 RAP samples taken across the state, and characterized for low temperature and high temperature grade [for Superpave mixes], they say. “New asphalt binder properties were obtained from more than 200 quality acceptance samples that covered three minus-22 grades and three minus-28 grades,” they said in January. “The data were analyzed to determine the maximum amount of RAP that could be added. Up to 22-percent RAP could be added without changing the original grade of binder. By shifting to a minus-28 grade, the allowable RAP increased to 38 percent. These findings supported the findings of a North Central Superpave Center study on five asphalt plants.”
The result was enough confidence in the existing RAP and its interaction with virgin PG binders that Indiana DOT was able to change its RAP acceptance specs upward. “On the basis of this information, INDOT changed the specification for RAP to allow up to 25-percent binder substitution without changing the normal binder grade of minus-22, and up to 40 percent if the binder was changed to a minus-28 grade.”
WMA and RAP
As WMA is an unfolding technology, its interaction with RAP is being studied in an ongoing investigation. The Effect of Warm Mix Asphalt on RAP in Hot Mix Asphalt is being undertaken by Rutgers’ Bennert and Nazhat Aboobaker of the New Jersey DOT.
The project is intended to determine how RAP can be used at typical and higher percentages in warm-mix asphalt. “One of the critical issues facing warm-mix asphalt is the lack of a formal mixture design procedure,” the researchers say. “If warm-mix asphalt is to replace or be used in conjunction with hot-mix asphalt in the future, a laboratory mixture design procedure for warm-mix asphalt must be established.”
Key issues that will be addressed during the research project are: the appropriate RAP percentages due to potential of decreased RAP and virgin asphalt binder blending with WMA; possible mixture design modifications for WMA technologies and additives, including foamed asphalt; possible recommendations for minimum production temperature and storage times of warm-mix asphalt; and acceptance procedures for allowing the use of current and new WMA technologies and additives. The project began Mar. 1, 2010, and is set to end April 30, 2012.
A Limit to RAP Content?
Use of larger quantities of RAP in highways might be attractive today due to the obvious savings in material costs, but that might lead to trouble “down the road,” say José P. Aguiar-Moya and Jorge A. Prozzi, Ph.D., University of Texas-Austin, and Feng Hong, Ph.D., P.E., Texas DOT, in their January 2011 TRB paper, RAP: Save Today, Pay Later?
In Texas, the DOT allows up to 30-percent RAP in base mixtures and up to 20-percent RAP in surface mixtures. “There are many advantages that are associated with the use of RAP, including economic benefits due to the reduction in virgin asphalt binder and new aggregates required, environmental benefits associated with the use of a recycled material, significant energy savings, and short-term performance benefits due to increased rutting resistance,” the authors say. “However, field observations have raised some concerns in terms of the long-term performance of mixtures containing RAP compared to those of virgin mixes.”
In order to address these concerns, the authors used data from FHWA’s Long-Term Pavement Performance (LTPP) project’s SPS-5 experiment in Texas to quantify and compare the field performance of pavement sections containing RAP to those of those that don’t.
Based on the SPS-5 data, simple performance models were developed for rutting and cracking of the pavement structure. The models were then used to statistically quantify the effect of RAP on each type of distress and to estimate the expected pavement life of a given overlay, with and without RAP.
“As expected, the results indicate that there is a significant gain in rutting resistance when using RAP,” the authors say. “However, pavements containing RAP develop cracking earlier, and at a faster rate, so short-term savings may be offset by additional overlays later in the life of the pavement. This raised the following concern: Are we saving today to pay later?”
The authors conclude that RAP may not be always the most economical solution, and that lifecycle cost analysis is imperative to assess the real benefits and costs of the various alternatives. “The interim results indicate that, under particular scenarios, the use of RAP might not be the most economic choice,” the authors say. “Where and how much RAP should be used should be determined through a case-by-case analysis.”
The authors don’t want to discourage higher amounts of RAP in mixes, but emphasize that pavement designers need to be cautious with the use of RAP and to take into consideration that pavement structures with RAP might deteriorate faster in the long run, mainly in cases where RAP is used in thin overlays.
“Increasing RAP percentages is not always the solution,” they write. “Consequently, it is important that proper deterioration models be developed and calibrated for the different regions where RAP is used so that proper economic analysis is applied for determining whether or not to use RAP in each specific project. Pavement managers should consider that using RAP today may result in initial construction savings, but the long-term maintenance and rehabilitation costs might overshadow these initial benefits.”
ETG Guides RAP Use
Also guiding the effort toward higher percentages of RAP is the Reclaimed Asphalt Pavement Expert Task Group, or RAP ETG. Created in 2007 by the FHWA, the RAP ETG is composed of materials specialists from FHWA, state DOTs, AASHTO, NAPA, NCAT at Auburn University in Alabama, and other stakeholders.
Its mission is to advance the use of RAP in asphalt paving applications by providing information emphasizing the production of high-quality, high-RAP mixtures, the performance of asphalt mixtures containing RAP, technical guidance on high-RAP projects and RAP research activities.
In September 2011, activity of the RAP ETG was the subject of an FHWA Tech Brief titled High Reclaimed Asphalt Pavement Use (the ETG defines high RAP as 25-percent or more RAP in an asphalt mixture by weight of the total mix).
The Tech Brief contains the latest responses to a biannual survey on RAP use conducted by the RAP ETG. With the assistance of AASHTO, the survey was conducted in 2007, 2009 and 2011. “In 2007, the typical hot-mix asphalt mixture contained about 12-percent RAP,” the document states. “From 2007 to 2009, about 27 states increased the amount of RAP permitted in asphalt mixtures, and, as of 2009, 23 states have experience with high-RAP mixtures. As of 2011, the majority of state highway agencies (more than 40) allow more than 30-percent RAP; however, only 11 report actually using 25-percent RAP or more.”
The RAP ETG Tech Brief also lists recent documents that articulate new technical information on higher RAP contents. Download it by searching for “FHWA-HRT-11-057.”
Earlier in 2011, the FHWA rolled out a definitive document that maintains that, based on an evaluation of pavements containing 30-percent RAP through the LTPP program, performance of pavements containing up to 30-percent RAP is similar to that of pavements constructed from virgin materials with no RAP.
The April 2011 report, Reclaimed Asphalt Pavement in Asphalt Mixtures: State of the Practice (Publication No. FHWA-HRT-11-021), provides new guidance on best practices when using RAP, and documented information about long-term performance of high-RAP pavements.
The state of the practice for RAP use across the United States, as well as common challenges for increasing the use of RAP, are identified. Authored by FHWA’s Audrey Copeland, best practices for the use of RAP are presented for developing specs, and for sourcing, processing, stockpiling, testing, designing, evaluating, producing and placing high-RAP mixtures. Ways to attain best performance for high-RAP mixtures are presented. Download the report by searching for “FHWA-HRT-11-021.”
When Politics Drives RAP Use
While other states adopt a tiered approach to higher percentages of RAP, California is using legislation to aggressively adopt higher RAP in HMA specifications.
The California Asphalt Pavement Association (CalAPA) reported in October 2011 that Caltrans’ acting director Malcolm Dougherty says the state transportation department is “moving aggressively” to adopt new standards to permit more RAP usage on state highway jobs.
The pledge comes as assembly speaker pro tem Fiona Ma is pressing Caltrans in legislation to allow up to 50-percent RAP in mixes. In an August 10, 2011 letter to Dougherty, Ma said she was “disappointed” by an earlier letter to her office from Caltrans indicating a lengthy process involved in evaluating a move to a higher RAP standard.
In his official response dated September 5, Dougherty said his department “recognizes the benefits of using a higher percentage of [RAP]. Caltrans is moving aggressively to introduce specifications and guidelines that will incorporate a higher percentage into our projects, while ensuring long-term performance of our paving materials.”
Dougherty announced that the department has accelerated an internal deadline, from June 2012 to November 2011, to develop a specification for 25-percent RAP, which will be incorporated into pilot projects in 2012 and evaluated. Current Caltrans specifications limit RAP to 15 percent of mixes.
“Industry’s reaction to the news was mixed,” CalAPA reports. “On the one hand, industry representatives were glad that Caltrans was recognizing the need to increase RAP limits, but the incremental approach and relatively slow pace of the changes bred frustration.”
CalAPA reported Bill Williams of Bo Dean & Co., an asphalt producer in Santa Rosa, as having said, “There is no known reason why Caltrans should limit high percentage RAP to 25 percent. I believe that 25 percent is achievable without fractionalization, especially when incorporated with warm-mix asphalt technology. Caltrans should not limit our ability to move toward a greener asphalt that creates better roads.”
RAP Basics
Reclaimed asphalt pavement – cold-milled using dedicated, high-performance machines that remove deteriorated pavement, improve overhead clearances and reveal curbs to enhance drainage – is one of the most recycled products in North America.
Stockpiles of RAP are commonplace at asphalt plants and even alongside construction projects. The self-propelled cutting machines mill off aged, cracked asphalt pavement in varying depths and widths, and convey the RAP to dump trucks which haul to stockpiles. From there, RAP is reused as inexpensive road base, added to virgin hot-mix asphalt as a tested material, used for driveways, bike paths, recreational trails and much more.
Asphalt pavement is unquestionably the nation’s most widely recycled product, reports the Asphalt Pavement Alliance, an industry coalition. APA says about 100 million tons of asphalt pavement are reclaimed each year during resurfacing and widening projects, and more than 95 percent of that total is reused or recycled.
Use of RAP saves valuable aggregate resources. While in America there are plenty of construction aggregates in place in the ground, virgin aggregate extraction sites are finding it more and more difficult to obtain mining permits.
Existing quarries or gravel pits once outside of a city now are being overwhelmed by new suburbs and neighbors who don’t like living near quarries and will fight any kind of expansion. This also puts the future supply of virgin aggregates at risk.
But RAP already contains existing aggregates that have been acquired, permitted, shot, loaded, crushed, screened, stockpiled, reloaded and hauled – at great expense – thus their reuse saves time, money and resources. Use of RAP also eliminates costly landfilling of the material, which was the practice prior to the popularizing of RAP use in the last two decades.
Moreover, big jumps in the cost of asphalt and asphalt paving – in addition to increased pressure for an environmentally sustainable transportation infrastructure – have boosted the use of RAP in asphalt mixes. RAP significantly lowers the overall cost of bituminous road mixes while providing substantial environmental benefits.
Higher use of RAP is another way to lower production of greenhouse gases in road construction, said National Asphalt Pavement Association president Mike Acott at a House hearing in 2009.
“Consumption of fuels in the process of acquiring and processing raw materials accounts for a significant share of the greenhouse gas emissions associated with producing asphalt pavement material,” Acott told the House in March. “Therefore, it is possible to reduce greenhouse gas emissions simply by incorporating RAP in new pavement.”