Spreading the Wealth
Asphalt emulsions mix oil with water
As pavement preservation techniques tighten their beachheads in state, county and municipal road agencies, new attention is focused on surface treatments, thin asphalt surfacings and the asphalt emulsions that make them possible.
Asphalt emulsions – mixtures of liquid asphalt and water – make expensive liquid asphalt go farther, covering far more square yardage and aggregate surface area for asphalt pavement preservation surfacings than possible with thicker lifts of hot or warm mix asphalt, all things being equal.
While they don’t add structural value, these thin surfacings aren’t intended to. Instead they protect aging asphalt pavements, seal cracks, retain aggregate, waterproof pavement structure, enhance friction, and with rejuvenators, give new life to an aged, oxidized asphalt surface. Emulsions used in full depth reclamation (FDR), though, can add structural value to a pavement structure.
“Asphalt emulsions are essential to all aspects of pavement preservation, be they recycling, micro surfacing, chip seals, or crack sealing,” says Mike Buckingham, director of pavement preservation, COLAS, Inc., and 2012 president, FP2 Inc. “Almost everything involved in pavement preservation is somewhat tied to emulsions.”
Asphalt emulsions make all this possible, yet they have a physio-chemical basis that in some ways is more complicated than plain bituminous pavements.
Everyone knows oil and water don’t mix. That is, unless they are emulsified, and the chemistry of the necessary emulsifiers is key to the successful application of asphalt surface treatments.
An asphalt emulsion is a homogeneous mixture of two insoluble substances, oil and water. In it particles of liquid asphalt (in the dispersed phase) are surrounded by molecules of water (the continuous phase).
Milk is one example of a liquid emulsion, in which globules of milk fat are suspended in liquid. Smoke is an example of an emulsion in which solid particles (carbon) are suspended in a mixture of gases (air).
Believe it or not, liquid asphalt is an emulsion. “Asphalt binder itself is an emulsion, even before you emulsify it,” says Andy Bickford, applications chemist, MeadWestvaco Corp., at the Asphalt Emulsion Technologies Workshop held in St. Louis in November 2011 by the Asphalt Emulsion Manufacturers Association. “Asphalt is composed of small crystal particles called asphaltenes, which are suspended in a continuous oily liquid phase generally classified as maltenes, meeting the definition of an emulsion. It’s the balance of the hard crystalline particles vs. the oil phase that determines things like asphalt grade and hardness.”
Why Emulsify Asphalt?
Because asphalt generally is solid at ambient temperatures, its viscosity must be lowered in order for it to be used. Energy can be added to the material to heat and liquefy it; solvents can be added to liquefy it; or it can be emulsified.
“When you emulsify asphalt, you are creating a vehicle that will transport asphalt without having to heat it, or use high mechanical energy to spread it in a thin layer, or coat the surface of a rock,” says Codrin Daranga, Ph.D., technical manager, Blacklidge Emulsions. “The water part or side of the emulsion is nothing more than a vehicle. It is used to get the asphalt in place, and then it’s gone.” And once the water is gone, all that’s left is the residual asphalt, traces of the emulsifier, and traces of other additives.
“We emulsify asphalt to reduce its viscosity to make it liquid at ambient temperatures,” Bickford says. “Benefits include reduced energy use and costs, as not as much heat is required to get the asphalt usable. Worker exposure is less as they are not exposed to vapors and fumes from either the asphalt itself, or from cutback asphalt solvents. And there is less opportunity for burn hazards and jobsite odor, which is important in residential areas.”
In addition, experts say, if you properly formulate the emulsion based on the kind of materials involved, the complete system will have long-term performance benefits that a conventional hot mix asphalt mix will not have. Lastly, emulsions allow expensive liquid asphalt to be spread more thinly, saving valuable road maintenance funds.
Powerful blenders or colloid mills create asphalt, or polymer modified asphalt, emulsions. The mill consists of two parts: a stationary element called the stator, and a rotating part called the rotor. A small gap separates the two, on the order of a millimeter in diameter, up to 75/1000 of an inch across. Hot liquid asphalt, water and an emulsifying agent are brought together in the mill, where the spinning blades of the rotor break or shear the liquid asphalt against the stator into suspended micro-droplets. The asphalt globules first elongate, then break into two or three smaller particles, which themselves break up into even smaller particles. The dwell time within the mill is measured in thousandths of a second.
The emulsifier – commonly a surfactant or surface-active agent – maintains the microscopic asphalt droplets in a stable suspension within the water, keeping them from recombining. Emulsifiers also control “break” time following placement on a road, in which the water evaporates, leaving the asphalt behind
“Anybody who works with liquid asphalt knows it sticks to everything,” Bickford says. “It also wants to stick to itself. The moment you produce the asphalt particles, and they are close to each other in the emulsion, they will try to stick back together, and the emulsion as separate particles won’t last very long.”
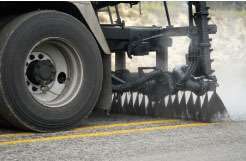
To keep the asphalt droplets apart, a chemical additive, or emulsifier, is used to coat the droplets, and protect them from each other. The average droplet size is from 3 to 7 microns in diameter, and asphalt usually is 57 to 70 percent of the emulsion, less than half being water, Bickford explains.
One gram of asphalt – about the size of a sugar cube, Bickford says – will form about 10 billion particles with a total surface area of 1 to 2 square meters, yet in an asphalt emulsion a third or less of the volume is water. The emulsifier must protect or stabilize all this material. “One drop of emulsifier will stabilize 100 billion particles, for a surface area of 20 square meters, or a 14-by-14-foot square,” Bickford says.
Chemistry of Emulsions
There are hundreds of emulsifiers available, each chemically a little different from the other, but they all have elements in common. Part of an emulsifier molecule is oil-soluble, and another is water-soluble. And the molecules will have a characteristic – most often an electrical charge – that keeps the asphalt surfaces from rejoining.
Typically the emulsifier molecule will be in the form of a head-and-tail, in which the long and skinny tail group is oil-soluble, with the properties of a hydrocarbon. The head will be water-soluble, with carbon and hydrogen atoms, but also contain nitrogen, oxygen or other elements. “It’s one big molecule, but has two different characteristics,” Bickford says.
“There is something about the nitrogen and oxygen that causes the head to want to hold an electric charge,” he adds. “Nitrogen kind of likes to hold a positive charge, and oxygen likes to hold a negative charge. And the charge makes the ‘head’ part of the molecule water-soluble.”
The oil-soluble tail portion of the molecule is derived from a fat source, for example, tallow or beef fat, or vegetable fat, like coconut oil. “These fats have chemically reactive sites on them that allow us to test the head groups and change the way they perform,” Bickford says. And that includes giving the head an electrical charge.
There are two main types of emulsions, cationic (positively charged) and anionic (negatively charged). Because like charges repel, droplets bearing the positive (cationic) emulsifier will repel each other, keeping them from recombining, thus providing a storage-stable asphalt emulsion product. The same is true for droplets bearing the negative (anioic) emulsifier.
Either way, the emulsifier producer applies the charge to the emulsifier molecule by making changes in the chemistry of the head section. This is accomplished by adding chemicals to the water, asphalt and emulsifier as it goes through the colloid mill.
Addition of the strong base sodium hydroxide to the mill produces a fatty acid sodium salt in the head with a negative charge, resulting in an anionic emulsion. When the materials are reacted with the strong acid hydrochloric acid, a fatty amide hydrochloride salt in the head with a positive charge, and a cationic emulsion, is produced.
Why use a cationic emulsifier instead of an anionic? Use of the right emulsifier ensures adhesion to aggregates. With rock chips used in chip seals, for example, the aggregates used will have a slight negative or positive charge; for good adhesion, use a cationic emulsion for stone that bears a negative charge, and anionic for stone that bears a positive charge.
Igneous chips of silicate mineralogy like granite, trap rock or basalt generally are negatively charged and react best with a cationic (positive) emulsion; positively charged sedimentary rocks of carbonate mineralogy like limestone or dolomite react best with an anionic (negative) emulsion.
The surface texture and microporosity of the aggregate will help the asphalt bond mechanically, whereas the chemical bond imparted by the negative/positive attributes seems to be more important when slick, siliceous gravels are used, which are best held with a cationic emulsion. Cationics tend to work with both good and bad aggregates, experts say; the anionics tend to work best with good limestone aggregates or those with lots of surface texture.
After placement on a pavement, the emulsified asphalt sets or “breaks” as the asphalt droplets precipitate or fall out of the water suspension and coat the aggregates. At this time the color of the emulsion turns from brown to black. As described by the Texas DOT, as more and more water is lost through evaporation, the particles are forced closer and closer together until they can no longer be separated by a film of water. At this point droplets coalesce into larger and larger drops and ultimately a sheet of asphalt on the road.
For rapid-setting emulsions, this process begins when they hit the chips. For medium-setting emulsions, the break starts sometime after mixing with the aggregate, depending upon the emulsion and the amount of fines in the aggregate. Slow-setting emulsions are very stable and normally break with the evaporation of the water.
Coalescence and Flocculation
The electrostatic charges on the heads of the emulsifier molecule sometimes may not be enough to keep the asphalt droplets apart. “The asphalt droplets in the emulsion have a small charge,” says Alan James, performance applications specialist, AkzoNobel Surface Chemistry, in his paper Overview of Asphalt Emulsion, Transportation Research Circular E-C102, Asphalt Emulsion Technology, August 2006.
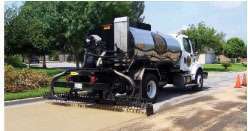
“The source of the charge is the emulsifier, as well as ionizable components in the asphalt itself,” James says. “These small charges on the droplets normally provide an electrostatic barrier to their close approach to each other (like charges repel). However, when two droplets do achieve enough energy to overcome this barrier and approach closely then they adhere to each other (flocculate). This flocculation may sometimes be reversed by agitation, dilution or addition of more emulsifier.”
That’s why it’s important to use asphalt emulsions soon after they are produced. “Over a period of time the water layer between droplets in a floccule will thin and the droplets will coalesce,” James says. “The coalescence cannot be reversed. Factors that force the droplets together such as settlement under gravity, evaporation of the water, shear or freezing will accelerate the flocculation and coalescence process, as does anything that reduces the charge on the droplets. Lower viscosity asphalts coalesce more rapidly than high viscosity asphalts.”
Nomenclature
An “alphabet soup” of letters designate the types of asphalt emulsions that are available, but it need not be confusing, as the letters correspond to the attributes of the emulsion.
Cationic emulsions begin with a “C.” If there is no C, the emulsion is usually an anionic, reports the Asphalt Institute (AI).
Emulsified asphalts come in rapid-, medium-, and slow-setting grades for different applications and are developed through the use of different emulsifying agents and the addition of some solvents. Still, their asphalt droplets particles will be either anionic or cationic. Rapid-setting emulsions are used mostly for chip sealing, while the medium- and slow-setting grades are used for emulsions mixes for recycling, fog seals or tack coats placed in advance of asphalt lifts.
After the charge designation, the next set of letters describes how quickly an emulsion will set or coalesce to a continuous asphalt mass. The standard terms are RS (Rapid Set), MS (Medium Set), SS (Slow Set), and QS (Quick Set).
“RS emulsions break rapidly and have little or no ability to mix with an aggregate. MS emulsions are designed to mix with aggregates, and are often called mixing grade emulsions,” according to the Institute. “MS emulsions are used in cold recycling, cold and warm dense-graded aggregate mixes, patch mixes and other mixes.”
SS emulsions are designed to work with fine aggregates to allow for maximum mixing time and extended workability, AI says. “They are the most stable emulsions and can be used in dense-graded aggregate bases, slurry seals, soil stabilization, asphalt surface courses and some recycling. SS emulsions can be diluted with water to reduce their viscosity so they can be used for tack coats, fog seals and dust palliatives. SS emulsions are also used as driveway sealers.”
QS emulsions work well with fine aggregates but are designed to break faster than SS emulsions. QS emulsions are used in micro surfacing and slurry seal designs. The quick break allows for faster opening to traffic.
An HF that precedes the setting time designation indicates a high float emulsion. Polymer-modified HF emulsions are made with a special family of emulsifying agents that leaves a gel structure behind in the asphalt residue, and were developed for low volume roads in areas where a graded cover aggregate is to be used, according to the Iowa Highway Research Board (IHRB).
“High float emulsions are also quite effective when used with somewhat dusty aggregates because they provide a thicker asphalt film on the aggregate and the aggregate can penetrate much more uniformly,” the IHRB says. “This is because high float emulsions are slightly anionic (sets slower than most cationic emulsions), and there is a small amount of solvents in them that act as a cutter in penetrating the dust. A thicker asphalt film coats the aggregate; therefore, high float emulsions do not flow and drain as readily as conventional emulsions.”
After the set designation, there is a series of numbers and letters that further describe the characteristics of the emulsions. The number 1 or 2 designates the viscosity of the emulsion, with the number 1 meaning lower viscosity and 2 meaning higher viscosity. If there is an “h” at the end of the name it indicates a harder base, whereas and “s” indicates a softer asphalt base. For example, SS-1h is a slow setting emulsion with a lower viscosity made from a relatively hard base asphalt, says the Asphalt Institute.
A “P” will be added to the set designation to show the presence of polymer in the emulsion. An “L” indicates the presence of latex polymer. Therefore CRS-2P is a cationic, rapid setting emulsion having a higher viscosity and containing some polymer.
Polymer-Modified Emulsions
The term “polymer” simply refers to a very large molecule made by chemically reacting many (poly) smaller molecules (monomers) to one another in long chains or clusters (see Chemistry of Asphalt Modifiers, April 2012, pp 16-27). The physical properties of a specific polymer are determined by the sequence and chemical structure of the monomers from which it’s made. When polymers are added to asphalt, the properties of the modified AC depend on two things: the polymer system used, and the compatibility of the polymer with the asphalt.
Polymer-modified emulsions provide enhanced performance at a higher price.
They will provide low temperature flexibility in pavement, stiffness at high temperatures, and extended surface treatment life. Like asphalt modifiers they include SBS (styrene butadiene styrene), SB (styrene butadiene), EVA (ethylene vinyl acetate), and many others, in which the polymer penetrates the oil droplet, and SBR (styrene butadiene rubber) and ground tire rubber (rubberized asphalt), in which the polymer exists outside the droplet.
Polymers in emulsions will increase early stiffness of the binder, which leads to a better early aggregate chip retention, according to the Iowa Highway Research Board. “When compared with non-polymer modified binders, the flexibility of the treated surface is increased in cold weather and over time is a result of the emulsion being modified with the addition of polymers.”
Bleeding and flushing of surfaces treated with polymer-modified emulsions is reduced in warm weather because polymers enhance binder stiffness at high temperatures. Polymer-modified emulsions also can be used to make stress-absorbing membrane interlayers (SAMIs) between lifts of asphalt.Polymer-Modified Texas Seal
Drivers in the San Antonio District of the Texas Department of Transportation (TxDOT) are benefiting from the use of a new polymer-modified asphalt emulsion for seal coats or chip seals that is providing longer-lasting surfacings and optimizing traffic flow through work zones.
Some 99 percent of San Antonio District pavements are surfaced with either chip seals – called “seal coats” in the local lingo – or asphalt lifts, says John Bohuslav, P.E., director of maintenance, TxDOT San Antonio District 15.
Today, a CHFRS-2P asphalt emulsion – which, following the guidelines above, is a cationic, high-float, rapid-set emulsion in the No. 2 viscosity range with polymer added – is solving adhesion and slow break problems endemic to lower-performance emulsions that had been experienced by the district.
“It’s from a local supplier, it’s easy to get, and it’s on our low-bid list of items to buy, as is the conventional CRS-2P,” Bohuslav says. “The difference between the two is the high-float characteristic that grabs the rock better. The guys like it, it sets well, and it grabs the rock and holds it. The work I’ve seen them do is outstanding, I think our crew does some of the best seal coats in the state.”
In addition to its better adhesion and durability attributes, the cationic emulsion allows the state to place seal coats on the hottest days, of which there are many in the San Antonio region.
“On hot summer days, when it’s in the 100 degree F range and we are trying to shoot seal coat, the anionic emulsions won’t break and set quickly enough,” Bohuslav says. “They just sit there. But the cationic will break and set much faster, so we can get the work done, finish and move on.”
For these important applications TxDOT’s San Antonio District is using a CHFRS-2P asphalt emulsion from Ergon Asphalt & Emulsions. It’s made possible by a polymer, Butonal NX 1122 from BASF.
“For years we’ve had both anionic emulsions with high-float structures, and cationic polymer-modified emulsions,” says Cary Brownlee, regional sales manager, Ergon Asphalt & Emulsions, Inc. “They represent a value-added product for chip seals with specific benefits to the user. CHFRS-2P marries the properties of both, resulting in a cationic emulsion with high-float attributes.”
Emulsions for Reclamation
Asphalt emulsions – polymer-modified or not – constitute an important alternative as a stabilizing agent for full-depth reclamation (FDR) of decayed asphalt roads, aggregate bases, and sandy soils.
“In my former role as a contractor, about 25 percent of the FDR work we did involved injection of asphalt emulsions to stabilize a base,” says COLAS’ Mike Buckingham. “These emulsions are an alternative to chemical additives like lime, cement and fly ash. Asphalt emulsions constitute one of the choices that a buyer agency has for a stabilizing agent.”
Despite being a value-added manufactured product, asphalt emulsions don’t represent a more expensive quantity than the commodity-priced bulk lime or cement. “Emulsions are not necessarily more expensive,” Buckingham tells Better Roads. “It depends on the makeup of what you are trying to stabilize, and what will build strength better to the level you are trying to achieve. If you are doing dirt or sand products you might be more apt to use a dry stabilizer with water, rather than emulsion. Otherwise we might use emulsion by itself, or in combination with the other products.”
Asphalt emulsion helps to increase cohesion and load-bearing capacity of the mix, according to the Federal Highway Administration (FHWA). It also helps in rejuvenating and softening the aged binder in the existing asphalt material.
“The advantage of using emulsion is that emulsions are low in viscosity and very suitable for application through an on-board liquid additive system in the recycling equipment,” FHWA says in its Pavement Recycling Guidelines for State and Local Governments. “After the blending of the base material and emulsified asphalt, the emulsion ‘breaks’ and water separates out from the asphalt cement. This water is forced out of the base during compaction or will evaporate out during the curing period. The resulting residual asphalt cement has high viscosity and, therefore, helps in improving the cohesion of the base material.”
Alternatively, portland cement increases base compressive strengths, lime mitigates reactive, expansive clay in base materials, and fly ash increases impermeability and strength of the recycled mix.
“Emulsion-treated FDR may be cheaper than dry chemical reclamation when considering the entire structure — reclaimed base plus overlay — as emulsion-treated bases have a higher structural value,” Buckingham says.
Cutting Back on Cutbacks
A different way of creating a thin asphalt surfacing material is by use of solvents to dilute the liquid asphalt. These “cutback” asphalts are blends of asphalt cement mixed with solvents, which make the asphalt cement fluid for spraying or mixing. The solvents then evaporate, leaving the base asphalt cement in place to bind stone or chips.
The use of cutback asphalts, once common for chip seals, has declined considerably because of environmental restrictions in specific regions around the country on hydrocarbon emissions from the evaporating solvents. Engineers are concerned with the use of cutback asphalt for surface treatments for environmental reasons, the presentation of fire hazard, and potential health risks posed to construction workers.
Cutback asphalts release of volatile organic compounds (VOCs) into the air, from the evaporation of the petroleum solvent used to reduce viscosity of the asphalt cement. VOCs can react photochemically with atmospheric NOx (nitrogen oxides) – in the presence of sunlight – to form ground-level ozone or smog. And the solvents used can be highly flammable and evaporative fumes can cause irritation among workers.
Like asphalt emulsions, cutback asphalts are classified as rapid-, medium- and slow-curing. Solvents used include gasoline for rapid-curing, kerosene for medium-curing, and diesel fuel for slow-curing cutbacks.
Likewise, pavement sealants or asphalt emulsions containing coal tar are losing favor and actually are targeted by legislation. For example, a bill introduced in the California Legislature in February would ban the sale and use of pavement sealant products that contain coal tar, classified as a carcinogen in high concentrations.
Sealants that use coal tar are in use in other states, primarily on the East Coast, and a bill to ban them nationwide, H.R. 4166, was introduced earlier this year in Congress by U.S. Rep. Lloyd Doggett (D-Texas.)
Engineered Rejuvenators
Rejuvenators are engineered cationic emulsions containing liquid asphalt components of maltenes and saturates (light fractions). They soften aged, stiffened, oxidized asphalt pavements, fluxing or fusing with the existing asphalt binder, changing the properties of the asphaltic concrete, quelling aggregate loss and extending surface life
According to manufacturer Tricor Refining, its Reclamite rejuvenator increases penetration values and reduces viscosity values. The rejuvenator, which is sold under the name Reclamite, seals out moisture and restores the asphaltene/maltene balance lost due to aging and oxidizing by replenishing the maltenes. The rejuvenator’s natural solvency is attributed to its naphthenic base.
The rejuvenator is spray-applied. The emulsion is diluted 2:1 (product to water) or 1:1 with water. Application rates are measured in square yards or meters and vary according to pavement absorption and application needs.
In 2005, Travis County, Texas, looked at the use of a maltene-based rejuvenator to improve and preserve its oxidized, cracked Type F mix low-volume street and road pavements. The county placed several full road-width test sections of the rejuvenating agent. They saw excellent absorption and penetration into the binder. Tests showed that the rejuvenator was fluxing with the binder, and results indicated a decrease in micro-viscosity of the binder in the range of 60 to 300 percent, along with a corresponding increase in penetration values.
The subdivision streets are vacuum-swept in 24 to 48 hours after application. A bonus is that because the rejuvenator does not contain asphalt, coal tar base or gilsonite, any tracking is kept to a minimum with little or no residential complaints.