Plumbed into the exhaust stream of many diesel powered off-road machines you buy today is either a diesel oxidation catalyst (DOC) or a diesel particulate filter (DPF) or both.
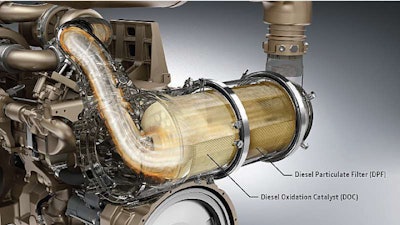
While there has been much talk and concern over these changes, the reality is that these engines and their emissions control systems are here to stay. Tier 4 Interim engines are more expensive. But for many of these engines the increased costs will be partially offset by gains in fuel efficiency and power. They are more complex, yes; but vastly better for the air we all breathe.
Your maintenance protocols will change little on these new engines. DOCs and DPFs, however, were not just stuck on to the exhaust ports of these engines as an afterthought. So when buying new equipment today you need to know:
• Does this machine have a DOC or a DPF – or both – selective catalytic reduction, or none of the above?
• What changes have been made to the engine upstream of the exhaust?
• How does my maintenance change as a result?
Downstream details
Depending on the horsepower category, some engines can get by without either a DOC or DPF, some use just a DOC, and a good many will use both plumbed together in line in a single canister.
In this arrangement the DOC is the first component to receive exhaust gas from the engine. “Under normal conditions the DOC reacts with exhaust gases to reduce carbon monoxide, hydrocarbons and some PM,” says Doug Laudick, manager of product planning at John Deere Power systems.
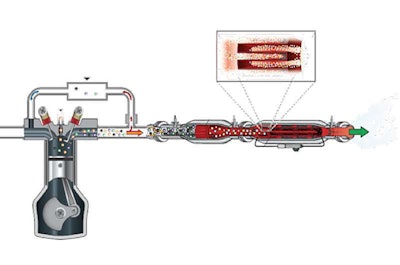
The DOC also protects the DPF. Hydrocarbon liquids or vapor can interfere with the DPF’s ability to trap and remove particulate matter, so manufacturers route the exhaust through the DOC first, then into the DPF, says Doug Mihelick, commercial manager, Large Power Systems Division, Caterpillar.
Some aftertreatment systems, however, require only a DOC, Mihelick says. And some manufacturers use a more heavily catalyzed DPF without a separate DOC. This type of system effectively operates as both a DOC and a DPF, he says.
The DOC is a flow-through device, forcing the exhaust over a honeycomb ceramic structure coated with precious metal. This chemically changes carbon monoxide and hydrocarbons to carbon dioxide and water, says Ray Schroth, director of service, Kubota Tractor.
In a combo unit, the exhaust gas leaves the DOC and enters the DPF. The DPF forces the exhaust gases to flow through porous channel walls, trapping and holding the remaining PM, Laudick says.
Trapped particles on the DPF filter element are oxidized (burned up) through a continuous cleaning process called passive regeneration, Laudick says. The heat of the exhaust burns away most of these particles but when that isn’t sufficient, additional heat can be generated in a process known as active regeneration. This may be activated with a change in timing or turbocharger output or a combination of these to increase the DOC inlet temperature before a small quantity of fuel is injected into the system.
Active regeneration will typically trigger a light on the machine’s dashboard, but will otherwise be transparent to the operator and not interrupt operation. Cold temps and long idle times increase regeneration frequency, but most manufacturers are calibrating the engines’ electronic control modules (ECMs) to application-specific parameters to keep the number of regens as low as possible. Active regens use some additional fuel, but since most of these engines gain fuel efficiency from electronic fuel injection, the impact on fuel consumption should be negligible.
One thing that causes confusion is that DPF is sometimes used as a common term for the whole DOC/DPF assembly, says Brad Stemper, manager, Case Construction Equipment. In most cases, the DOC is used in conjunction with the DPF, particularly because the DOC supports heat creation to burn off the PM collected within the DPF. And because the DOC creates this heat, it is located in front of the DPF, he says.
Maintenance changes
DOCs are maintenance free and designed to last the life of the engine, as long as you use ultra-low sulfur diesel fuel. The sulfur in non-ULSD fuel will “poison” the catalytic coating on the inside of the DOC and decrease its effectiveness, says Dave Hahn, manager, Hauler/Loader/Power Train Customer Solutions Team, Volvo Construction Equipment.
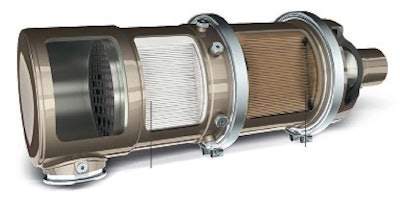
This is not a problem in the United States, Japan and Europe, though. You can’t even buy high sulfur diesel here anymore. But most of the rest of the world still has high sulfur diesel fuel. To contend with this, some engine manufacturers are developing conversion kits, others are producing two versions of their engines.
The major impact this will have on U.S. contractors is that it may make equipment with advanced emissions aftertreatment more difficult to sell at auctions where there are substantial numbers of buyers from countries with high-sulfur fuel – and that includes most of Latin America. (We will address this issue, and manufacturer’s attempts to create a “one-world” engine in more detail in a future issue of Equipment World.)
Ash loads and CJ-4
The new DOC/DPF technology also requires the use of low-ash oils, sometimes called low SAPS (sulfated ash and phosphorous) oils. These are designated by the American Petroleum Institute’s API CJ-4 label on the containers or spec sheets.
Ash is a natural component of lube oil and all engines burn a small amount of oil. Ash, unlike the PM or hydrocarbons, can’t be burned off, so it slowly accumulates in the DPF. The lower the ash level in the oil the longer it takes to accumulate.
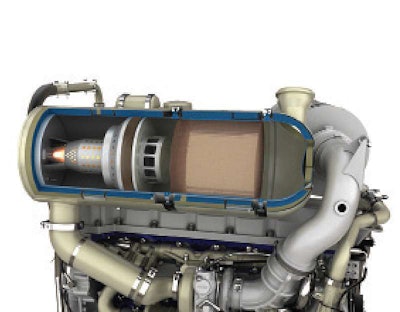
Once the ash load reaches the point that the aftertreament can’t do its job, the DPF is pulled from the machine and replaced with a new DPF or cleaned in specially designed equipment at the dealers. The EPA set guidelines for these engines, requiring DPFs that could handle the ash load for a minimum of 4,500 hours for engines 174 horsepower and up and 3,000 hours for engines below 174 horsepower, says Hahn.
This is the only major service interval change for these new aftertreatment systems, and while it is expected that a DPF cleaning or replacement will cost several thousand dollars, most manufacturers say they are exceeding the EPA minimums by a large margin.
“What we’re seeing with engines at 8,000 and 9,000 hours is that we’re nowhere near 100 percent ash load,” says Hahn. “Experience is telling us that that if correct operating and maintenance procedures are followed, with the correct oils and fuels, the DPF can last as long as 15,000 hours before it has to be cleaned.”
Not all in the exhaust
The componentry described above is collectively called exhaust aftertreatment. But engine manufacturers have been changing the engine designs upstream of the exhaust valves as well. The goal is deliver the fewest possible emissions to the aftertreatment and reduce the burden on the DOC/DPF, or in some cases, eliminate one or both devices. As a general rule, the smaller the engine, the easier this is to do.
Manufacturers have a variety of technological tools upstream from the exhaust that they can tweak to meet the emissions goals. And it seems no two engine manufacturers are doing it exactly alike. Many of these upstream changes came with the introduction of Tier 3 engines in the larger horsepower bands. But where it makes sense, these design changes are also migrating to the smaller horsepower engines as well.
For example, Kohler Engines looked at the aftertreament technology available and decided a large DPF would not suit the design parameters its customers were looking for in the 74-horsepower-and-below category. Instead, they started from scratch to replace their mechanical fuel injection with high pressure common rail fuel injection, says Jeff Wilke, Kohler Engines product manager for diesel product in North America. They also added a four valve head, a charge air cooler for the turbo and cooled, electronic EGR. For reduced oil consumption and less particulate matter a lot of development went into the engine block – a sophisticated design for a smaller engine, but the result was an engine that didn’t need a DPF and offered improved power, torque and fuel efficiency.
Kubota’s Schroth notes that engines with less than 25 horsepower have had to meet Tier 4 standards since 2008 and most manufacturers, Kubota included, comply without the need for DPFs or DOC. In the 75-horsepower-and-up range, Kubota is using a combination of DOC and DPF in conjunction with exhaust gas recirculation and common rail diesel technology, he says.
Deere’s PowerTech M 2.4L and 4.5L engines and PowerTech E 2.4L models (which range from 48 to 74 horsepower) have met Tier 4 Interim without DOC/DPF filters. Above that, though, they go with DOC/DPF aftertreatment.
Volvo hits the Tier 4 targets with DOC/DPF aftertreatment above 74 horsepower and DOC only in their compact line, says Hahn.
Case uses exhaust gas recirculation only in horsepower applications ranging from 48 to 74 horsepower, says Stemper. For many models in the 75 and higher horsepower range Case uses cooled EGR plus DOC/DPF. Case is also leading the way in off-road emissions control with selective catalytic reduction technology in its F-series wheel loaders for Tier Interim. “For Case, the decision to use one solution over another is not based on horsepower, but on each model’s engineering characteristics and application requirements,” he says.
Several other manufacturers have announced they will also have a SCR solution in time for the Tier 4 Final regulations. We’ll do a more thorough treatment of that subject and look more closely into the specific technology mix from each manufacturer in future issues.