Cool, Clean and Dry
Today’s construction machines perform at levels unheard of only a few years ago, thanks mostly to advances in hydraulic pumps. But with their high pressures and close tolerances these pumps require you to step up your game when it comes to maintenance and contamination control.
Keeping your hydraulic fluid cool, clean and dry isn’t rocket science, but it does require vigilance and knowledge of what’s going on inside the system. Failure to do so almost certainly will result in costly repairs (tens of thousands of dollars) and extensive downtime.
“There is a misconception that machines that have a sealed system and filters should run clean from the beginning until it’s time to replace the filters and oil, but that is not the case,” says Diego Navarro, service marketing manager, at John Deere Construction and Forestry.
Normal operation will admit small amounts of external contamination. And hydraulic fluid over time oxidizes, the additives degrade and the fluid picks up a certain amount of wear metals – all to be expected and cured with new oil and filter at the scheduled maintenance interval. But there are plenty of other sources of external and internal contamination you have to guard against as well.
EXTERNAL CONTAMINATION
Uncorrected leaks. “If you have a cylinder that’s leaking, it’s guaranteed that you will have dirt or humidity in the system,” Navarro says. “If leaks can get out, dirt can get in.”
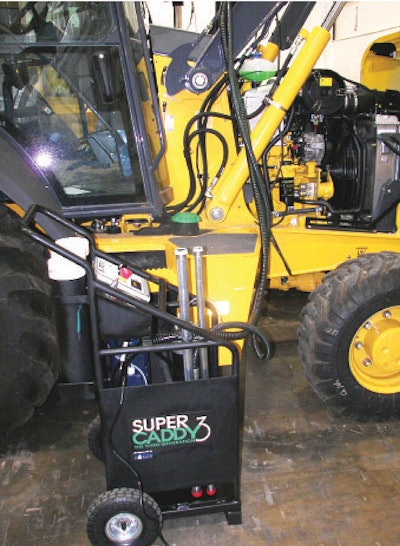
Service practices. How clean is your service truck and its containers? Do you filter the fluid before it enters or leaves the truck? Are your funnels, rags, service equipment clean? Even something as simple as repairing or replacing a hose can introduce significant contamination.
Attachments. Hydraulic hammers can put a lot of wear metal and sometimes dirt into the fluid. All it takes is a few minutes of operation for the dirty fluid in the hammer – or any other attachment – to circulate into the host machine’s hydraulic fluid system. Cross contamination between machines is also feasible when they share the same implement.
Mixing. Not all hydraulic fluids are alike. If you top up or refill with a different spec fluid you could seriously compromise to performance of the fluid.
INTERNAL CONTAMINATION
Wear metals. Like engines, hydraulic pumps wear over time and the fluid will pick up trace amounts of iron, copper, lead and other metals.
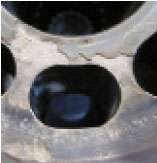
Resident contamination. Most machines come with clean fluid from the factory, but with hundreds of feet of hydraulic hoses and lines and multiple pumps and cylinders there is always the chance that some contamination may reside in the machine upon delivery. This shouldn’t be enough to warrant remedial action, but it does add to the cumulative total over time.
Catastrophic failure. Should a hose or seal break down, or a component within a hydraulic pump disintegrate, the residue will quickly spread throughout the system. A catastrophic failure on the slipper side of the pump is less severe than one on the pressure side of the pump.
Varnish. This is created when you have a high pressure leak that produces foaming and high temperature in the fluid. In these conditions micro-dieseling occurs (something similar to cavitation). Micro-dieseling in the presence of iron particles (catalyst) gives you varnish. Varnish particles are very small and can stick to sump and valve parts compromising their performance. Navarro says varnish isn’t too common, but he compares it to cholesterol in humans. “You have to clean it and fix the machine,” he says. “Sometimes you can save the machine from major damage, but typically people react, when the pump is already in trouble and it’s too late.”
OIL SAMPLING AND ANALYSIS
As with engine oils, sampling and analysis is the key to identifying these problems and figuring out a solution.
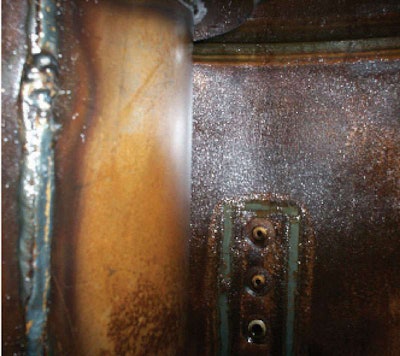
Since hydraulic fluid isn’t contaminated with combustion byproducts like engine oil, it lasts longer. The typical change interval can be anywhere from 1,000 to 4,000 hours. But you should sample much more frequently than you change hydraulic fluid. Navarro recommends it every 250 hours, as do many OEMs. At a minimum you should sample every 500 hours.
Mark Minges, chief operating officer for POLARIS Laboratories, recommends monthly sampling for any system or component that is critical to your operation. But, he admits, quarterly sampling is more typical.
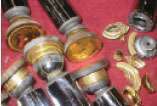
Monitoring wear is important, Minges says, but the real advantage to testing hydraulic fluids is to keep them clean enough to prevent valves from sticking, moving parts from wearing and dry enough for optimum system performance.
Minges adds that you should test viscosity, which indicates oxidation and fluid degradation. And check the acid number, which is relevant if the fluid is stressed, he says.
Who is Karl-Fischer?
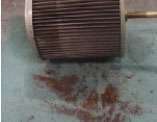
Water is the second leading killer of hydraulic pumps and also a major item to check in hydraulic fluid analysis. Water more than 500 parts per million can be detrimental to hydraulic system operation, Minges says. Water more than 1,000 ppm will cause corrosion and give the controls a spongy feel or make them unresponsive.
“The Karl-Fischer test allows you to see water below 100 ppm,” Navarro says. “The infrared test normally offered is blind to water until it’s about 1,500 ppm. So your visibility of water without Karl – Fischer is limited.”
Navarro cautions that some fleet managers underestimate the importance of water detection, or balk at the cost. “If you’re going to spend $10 for a regular sample or $13 for one with Karl-Fischer, I would do it with Karl-Fisher,” he says.
CHANGING AND FILTERING OIL
Hydraulic oil filters on your machines guard against a lot of the contamination you’ll encounter in normal operating conditions. But there are several ways to improve on that process as well.
Bypass filters. These are popular options in some applications and machines. A bypass is nothing more than a secondary filter that takes a small amount of oil and super cleans it before returning it to the sump. This super clean oil continually raises the cleanliness of the whole system. “Some people worry that with a bypass filter you won’t see wear,” Navarro says, “but you’ll see it on your oil analysis, although the threshold needs to be adjusted.”
Fluid caddies. These carts range from $2,000 to $10,000 and are used to siphon old fluid out of the hydraulic system, clean it to a desired spec and then return it to the machine. The more expensive versions measure the fluid cleanliness and continue to filter the oil in the system until it reaches a target level of cleanliness. The lower cost models simply work for a designated period of time. (See the resource box at the bottom of the page for more information on manufacturers of these carts.)
Flushing calculator. On engines when you drain the lube oil you remove about 95 percent of it. When you drain a hydraulic system, you only capture about half. The rest remains in the hundreds of feet of hoses and the pumps and cylinders. A flushing calculator is an Excel or spreadsheet type program that shows you how many times you have to flush and refill the hydraulic reservoir to get the whole system back to 95 percent or better. The numbers will vary with the size and type of machine, but in general you have to flush the system three times to get to 98 percent purity, and six times to get to 100 percent. Talk to your OEM dealer or lubricant supplier about getting a flushing calculator for your machines.
See our interview about today’s hydraulic oil filtration standards in our digital edition:
RESOURCES: FLUID CARTS
Pall Corporation: www.pall.com
Trico: www.tricocorp.com
Hydac: www.hydacusa.com
Internorman: www.internorman.com
Stauff: www.stauff.com