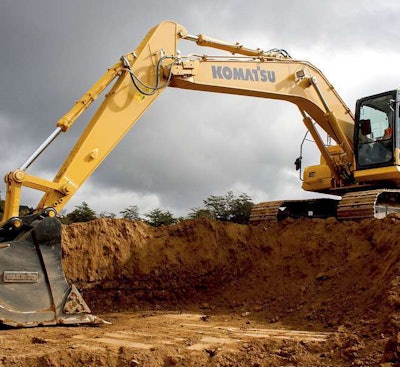
Komatsu PC210LCi-10
What does semi-automatic mean?
Komatsu wants to make clear the machine control takes over only when an operator nears the target surface as defined by downloaded project files. “When the bucket reaches the target design surface, the automation limits it from going below grade, even allowing semi-automatic tracing of the target design surface,” says Jason Anetsberger, Komatsu America project marketing manager, intelligent machine controls. In all other areas, operators are in complete control, and they can opt for manual controls at any time. “The fundamental design challenge was how to smartly add automation to increase the efficiency of the machine without limiting the productivity of an experienced operator,” Anetsberger explains.
“Productivity gains depend on the operator, who still controls the speed of the operation. This will raise an operator’s efficiencies, whatever his experience.” The company also wants to differentiate this system from what it calls “conventional guidance systems” now available for excavators. “With conventional guidance, the grade quality depends on the skill of the operator,” Robson says. “When you talk to customers, one of the biggest problems they had with these systems is speed. The operator is always constantly monitoring the indicate-only system to see if he’s on grade. With Intelligent Machine Control, the operator can focus on moving materials efficiently – and with plus/minus 42-millimeter accuracy – without worrying about meeting the target.” “This actually empowers the operator,” Anetsberger adds. “He’s not relying on people outside of the machine to tell him whether he’s on grade, and he has less tunnel vision than if he was constantly looking at a machine guidance monitor.”
How it’s done
The excavator’s Intelligent Machine Control system – modeled in part after Komatsu’s intelligent dozer line introduced last year and developed concurrently with the dozer controls – offers real-time bucket edge positioning in relation to the machine and job surface. The system has several components, all factory installed:
- Stroke sensing hydraulic cylinders on the boom, arm and bucket. Each of these cylinders has a built-in stroke sensor, providing real-time bucket position data sent to the in-cab control box. Monitoring displacement of the cylinders, the sensors track where the cutting edge of the bucket is relative to the body of the machine.
- An Inertial Measurement Unit, located inside the machine, which detects machine orientation.
- Working from project files, a 12.1-inch tablet-like touch screen display control box inside the cab shows side and aerial views of the machine, and uses a facing angle compass, a light bar and audio guidance.
- Two GNSS antennas, positioned on easily-accessed handrails behind the cab. A GNSS receiver is located inside the machine.
The only obvious clues an intelligent machine is different from the standard PC210LC-10 are the antennas and in-cab control box. All other components are internal. These components give the excavator these semi-automatic capabilities when near the target surface.
- Auto grade assist, in which the boom adjusts the bucket height automatically when the operator moves the arm, allowing him to trace the target surface and minimize digging too deep.
- Auto stop control, which stops the machine during boom or bucket operation when the bucket edge reaches the target surface, also limiting over-excavating.
- Minimum distance control, which controls the bucket by automatically selecting the point on the bucket closest to the target surface regardless of machine position.
Even if the machine is inclined while working, the facing angle compass ensures the machine is facing perpendicular to the target surface.
Touch controls
The 7-inch standard display in most excavators wouldn’t convey all the information operators needed with the Intelligent Machine System, so Komatsu opted for a 12.1-inch-high screen that uses a touch screen interface instead of a multi-step menu. (Note: the machine still uses the excavator’s function display monitor for regular functions.) The angle and magnification of the 3D display can be changed, allowing
“While this seems easy, it can be quite difficult, especially when you consider the machine is sitting on an uneven surface.” In a narrow column on the left side of the screen, a conventional colored light bar shows the bucket edge position relative to the target surface; when the buttons are green, you’re close to grade. Operators can also opt to use a sound function, which audibly warns them when the bucket reaches programmed distances from the target surface. If you opt for manual controls, the Auto mode can be turned off by pushing the upper right corner switch, putting the display in indicate-only mode.
If owners opt to use Topcon’s Sitelink 3D Enterprise system, machine and office can be connected in several ways: • Project files can be directly downloaded from a contractor’s office to the machine.
- Progress information and as-built data can be sent back to the office.
- Machine and office can send messages to each other.
- Machine functions can be remotely troubleshooted.
ROI in 18 months While not disclosing the exact number, Robson says there’s a “significant premium” for the Intelligent Machine Control system, but says Komatsu expects users to get an ROI in 18 months. As with the dozer, where the initial D6li-23 model opened the way for several intelligent dozers, the excavator intelligent controls are scaleable, and will most likely appear in larger excavators in the next 12 to 18 months.