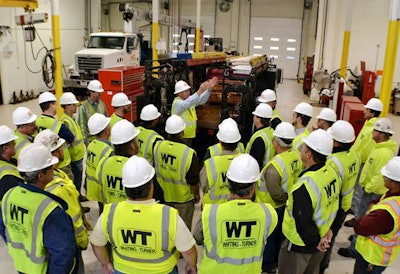
There are many small contractors out there looking for safety training information on a daily basis, which leads one to believe their company safety programs might not be as up-to-date as they would like.
If you’re using an inadequate or outdated program, it’s time to step up and develop your own—one that’s specific to your business that mirrors your scope of work.
So, how do you go about creating and implementing a new safety program? Depending on the resources available to you, there are several paths you can take.
Outsourcing
If you have the budget, you can have a safety consulting firm build a custom program for you.
They’ll take input from all levels of your firm, develop simple-to-follow work procedures and conduct periodic evaluations. You can also work with your insurance carrier and with local associations to develop a semi-custom program for your firm.
Adapting
If you’ve inherited or purchased your company, there was probably already a program in place. Perform an objective assessment of the program, determining what areas are workable for your firm today, and what areas need to be updated.
If you need help, consider OSHA’s free onsite consultation program. The services are separate from the enforcement division and will not result in penalties or citations.
As part of the consultation, OSHA will identify workplace hazards, provide advice on compliance and assist in establishing injury and illness prevention programs.
Creating from scratch
If you decide to start from scratch and create a program on your own, your safety program will need to include the following five components—management commitment and planning; employee involvement; worksite analysis; hazard prevention and control; and safety and health training.
In addition to general information, which can be found here, you’ll need to include job-specific training such as confined spaces or trenching that applies to the scope of work you perform. You can find customized programs to use as a guideline here.
………………………..
Of course, writing the safety program isn’t the same as implementing one. Once completed, either you or your designated safety manager must train the employees on the program, ensuring they have familiarized themselves with the requirements of the program.
Each employee should be issued their own safety manual, and sign and date a document indicating they have received and understand the material. Each time a safety meeting is conducted, a copy of the material should be give to the employee to retain in their manual and a written record of the meeting’s attendees should be kept.