How Chicago DOT Deals with the New Budget Realities
The Mission: Manage more than 6,000 miles of roads and alleys with less money and be greener about it.
The solution: Innovate and change.
The Great Recession has wreaked havoc in road management programs all over America, but it has also encouraged road professionals to re-evaluate traditional practices and replace some of them with more innovative, cost-effective solutions.
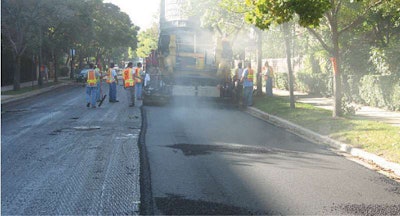
Road departments for small- and medium- sized cities and counties have been on the leading edge of this trend, their size and closeness to the citizenry making possible quicker, nimble reactions to changing economic tides.
But large and very large departments are changing, too, and the Chicago Department of Transportation is an excellent case in point.
In a city with a reputation for machine politics, change is in the air and it’s being felt in the Chicago DOT. The impetus for change comes from the city’s new mayor, former Obama Administration Chief of Staff Rahm Emanuel, as well as the rigors of the recession.
“Our directive is to stretch our budget and be environmentally friendly,” Chicago DOT Commissioner Gabe Klein told Better Roads at the site of a demonstration project last fall. “We’re not afraid to try new things.”
And indeed, the department is trying new things.
Investigating techno-solutions
Chicago DOT is looking for new cost efficiencies in the field and in the administration of contracts, says Quality Assurance Manager Cindy Williams, a department spokeswoman on pavement issues. She notes that the department wants to make a substantial upgrade in its pavement management system — without the financial pain of investing in a new, customized system.
“We’re reaching out to the Cook County Highway Department to see if we can adapt their systems,” says Williams. “We need a better system for asset management, one that lets us better track pavement age and condition, and helps us identify maintenance windows.”
Illinois’ Cook County takes in all of Chicago and dozens of close in suburbs as well as unincorporated areas. The county has its own vast network of roads and rights of way to maintain. Chicago Mayor Emanuel and Cook County Board President Toni Preckwinckle are looking for synergies between the two government entities, says Williams, and the County’s pavement management system may be one of them.
New pavement approaches
At the tactical level, the city is stretching its pavement management budget by changing the mill-and-fill specification for its 2012 arterial resurfacing program.
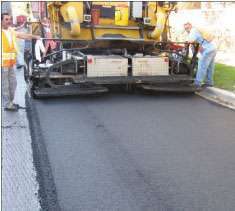
Chicago’s traditional approach called for milling 2-1⁄2-inches deep, then filling with a special 1-inch binder course, and a 1-1⁄2 -inch surface course. Department engineers refer to the binder course as a “IL 4.75 sand mix,” a very dense blend of manufactured fine aggregate and a high ratio of performance-grade, polymer-modified asphalt. “It reduces the pavement’s permeability and it reduces reflective cracking,” explains Williams. “But it’s very expensive.”
To get more lane miles of resurfacing from its 2012 budget, the city is going to a conventional single-lift mill-and-fill design.
If that seems like a step backward, keep in mind that some of the mix designs the city is employing are anything but traditional. In particular, Chicago is one of Illinois’ most aggressive road departments in embracing Illinois DOT’s mix designs for high-recycle content in its asphalt pavements. The state now has specifications allowing up to 40 percent of the liquid asphalt binder in a mix to be “replaced” with the residual asphalt binder found in recycled materials. To achieve the highest amount of recycled material allowable a mix design must incorporate both recycled asphalt shingles (RAS) and fractionated reclaimed asphalt pavement (FRAP).The recycled material can include up to 7-½ percent RAS as a portion of the liquid asphalt, and to achieve the highest RAP content the mix designs require utilizing fractionated RAP.
“We have a huge supply of RAP and RAS available in this area,” says Williams, “and we see this spec as an opportunity to be more cost-efficient and greener at the same time.” The FRAP specification includes a PG 58-28 liquid asphalt to provide a longer lasting mix and enhance the workability of the mix.
“Ultimately,” Williams explains, “the new IDOT specification encourages multiple sources of recycled content and it increases the potential amount of recycled content, as well as the quality and consistency of the mixtures. It gives the contractors and producers options. And by allowing multiple sources of ingredient materials, the end product is not held hostage to variations in any one component.”
Looking for concrete solutions
While the department is emphasizing pavement maintenance and preservation in these difficult times, the city’s engineers are also exploring options for reconstruction and replacement. Some of Chicago’s low-traffic volume pavements are decades past their design lives, Williams notes, so reconstruction is sometimes an unavoidable option.
For better or worse the city has traditionally favored composite pavements — concrete with an asphalt overlay — but they are exploring a variety of options for dealing with the rigorous climate and traffic demands. These options include full-depth asphalt and in-place recycling, but perhaps the most interesting is the employment of roller-compacted concrete (RCC).
“We placed a trial RCC pavement on a residential street last fall,” says Williams. The opportunity arose when the city water department needed to replace a sewer beneath the street.
First impressions of the trial were promising, says Williams. The process produces what promises to be a strong pavement at a cost lower than conventional concrete.
“The key to strength is getting density,” Williams notes. “We got that, and the pavement had strength in 48 hours. In fact, the RCC was at 3,500 psi in 24 hours!”
No pavement option is a panacea, however, and the city is concerned about public acceptance of RCC’s darker and more unconventional concrete appearance.
“We’re thinking of it initially as a base for a composite pavement,” says Williams. Engineers are considering a special thin-lift asphalt mix design as a surface course, modifying its sand asphalt mix with larger RAP fractions to optimize smoothness and traction.
Administrative solutions
Like local government agencies everywhere, Chicago DOT is looking for new cost efficiencies at the administrative/managerial level, too.
With thousands of miles of streets and alleys to manage, one of the biggest opportunities for savings is better coordination with the public utility companies that manage water, sewer, electric and gas infrastructure located beneath city pavements.
Williams acknowledges what all road departments know: Pavement restoration is expensive and disruptive, and there is a lot of potential savings if the department and the utilities can coordinate to minimize interventions. In Chicago, both the water/sewer department and People’s Gas have accelerated utility replacement programs underway, so the DOT is coordinating closely with them to maximize efficiency in restoration and to improve mapping of utility locations.
Chicago DOT is also experimenting with reverse auctions online for letting contracts. The department’s initial foray into these waters is a series of contracts for median and boulevard landscape and maintenance services this year. Contractors will have an opportunity to bid on the work knowing the amount of the current lowest bid.
“If we can save money with the reverse auctions,” says Williams, “we’ll use them for other kinds of contracts.” Discussions are underway to determine if that format will help attract bids for contracts such as supplying portland cement concrete for the city’s paving crews. She adds that other city departments are using the format, too — to purchase new police cars, for example.
Among local government road departments, Chicago DOT is different in many ways, from its sheer size and the complexity of its mission, to its heavy use of composite pavements and its enthusiastic embrace of high ratios of recycled materials. But the challenges the department faces are the same almost everywhere: Do more with less…and do it better.
Producing a 100-percent Recycled Surface Lift
On a chill Chicago morning last November, several dozen people clustered along an ancient residential street to watch a two-machine recycling process convert the road’s pock-marked,
Such is the promise of Gallagher Asphalt’s new Re-HEAT in-place asphalt recycling system.
Conventional hot-in-place recycling systems heat the asphalt surface to a workable temperature, then use tines to scarify it to a predetermined depth, mixing in fluids to rejuvenate the old asphalt cement as the HIR train moves along. The hot asphalt is then bladed to a smooth surface and correct grade, and compacted. The recycled pavement is covered with a surface treatment, usually a thin-lift hot or warm asphalt.
Gallagher’s Re-HEAT system employs the same heating technology to slowly heat the pavement to a workable temperature, then, instead of scarifying it, the system uses a moldboard and auger to pick up material at a pre-set depth and move it into a drum where it is mixed thoroughly with a rejuvenating fluid. The rejuvenated mix exits the mixing drum in front of the asphalt screed, then placed and compacted to specifications.
The result, says Gallagher, is a finished pavement that needs no surface treatment, can be opened to traffic in short order, and has a projected service life of a decade or more, assuming the original pavement was adequate for the current and future traffic loads.
Based in south-suburban Chicago, Gallagher Asphalt is one of the largest asphalt producers in Illinois, and one of the leaders in heat scarification HIR, both in its home state and nationally. The Re-HEAT system will add to the diversity of solutions the company offers, says Patrick Faster, national sales director of the company’s hot-in-place recycling operations.
“Compared to a conventional mill and fill, it saves a lot of time and a lot of money. It also costs less than heater-scarification HIR and an overlay,” says Faster.
Dan Gallagher, who owns and operates Gallagher Asphalt with brother Patrick and cousin Charlie, notes that there are applications where heater-scarification HIR is the better fit. “If the existing pavement structure needs to be stronger, the overlay of virgin mix that comes with heater scarification is the better option,” he points out.
Chicago Department of Transportation officials watching the demonstration project were enthusiastic about the concept and interested to see the results. Along with the potential cost savings, Gallagher Asphalt quotes a study that indicates Re-HEAT has a 63-percent smaller carbon footprint than a conventional 2-inch mill-and-fill and fill using 20 percent RAP in the mix — the benefits of eliminating virgin materials and delivery trucks.
As the first outing for Gallagher’s Re-HEAT equipment, the Chicago demonstration project made good on much of the system’s promise while also showing its main challenge. On the impressive side of the ledger, operating in cool weather and on a pavement that may have been older than many of the onlookers, the new recycling train produced smooth, tight asphalt to a depth of 1.5 to 1.75 inches. Densities were reading in the 93- to 94-percent range and the recycled surface was opened to traffic a short time after the HIR train passed.
On the “challenge” side of the ledger, there were several instances when the recycling machinery hit segments of oil-rich road patches and produced thick clouds of smoke and fumes, reminiscent of the early days of HIR applications several decades ago. This is not likely to be a persistent problem with the Re-HEAT system, the Gallaghers say, pointing out that the Re-HEAT heating technology is identical to time-proven heater-scarification equipment. The smoke on this demonstration project resulted from an unusual degree of variation in the surface asphalt content, the cool weather conditions, and a crew just getting familiar with new equipment.
Perhaps the ultimate view of the project came from several residents on the street, who turned out to thank the crew, the DOT officials and their alderman for the miracle being performed on their street. Few would have lived there long enough to remember when the road last had a smooth, new surface.