A system that allows detection of thermal segregation in the asphalt mat, in real time, and records a thermal profile is now being used by some state Departments of Transportation. The reason is to eliminate inconsistent densities because freshly paved asphalt pavement doesn’t compact properly after becoming too cool, and the low temperatures contributed to these low densities.
How well a machine will conform to the hauling and spreading operation are also considerations, and climatic and traction conditions are also important.
There is no single compactor that will do all things in all applications. Each type has a definite material and operating range on which it is most economical. In many cases, there are applications where machines of different sizes and types can achieve the compaction target; but choosing the machine that is most suitable will complete the work most economically and efficiently due to reduced passes, reduced fuel use and less working time.
Vibratory Compactors
Vibratory compactors work on the principle of particle rearrangement to decrease voids and increase density and load bearing strength. They come in two types: smooth drum and padfoot drum. For increased versatility, smooth drum compactors can be equipped with optional padfoot shell kits, which allows the use of smooth drum rollers in padfoot applications, albeit with limited performance.
Smooth drum vibratory compactors generate three compactive forces: static pressure, impact and vibration. Padfoot drum machines generate the same forces, plus they also generate manipulative force. Vibratory compactors provide uniform compaction throughout the lift.
Density is achieved from the forces generated by the vibrating drum hitting the ground. Compaction results are a function of the frequency and amplitude of the blows, as well as the force of the blows and the time period during which the blows are applied.
The frequency/time relationship accounts for slower working speeds on vibratory compactors. Working speed is important because it dictates how long a particular part of the fill will be compacted. For vibratory compactors, a speed of 1 to 2.5 km/h (0.6-1.6 mph) for rock and clay, and 2 to 5 km/h (1.2 to 3 mph) for gravel and sand will provide the best results.
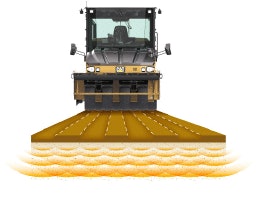
Smooth drum vibratory compactors were the first vibratory machines introduced. They are most effective on granular materials with particle sizes ranging from large rocks to fine sand. They are also used on semi-cohesive soils with up to 50 percent cohesive soil content. Lift thicknesses vary according to the size of the compactor. Whenever large rock is used in the fill, the lifts may be very thick—up to 1.2-m (4-ft.) lifts are not unusual. One thing to remember when large rocks are in the fill is that the thickness should be about 300 mm (12 in.) more than the maximum rock size. This permits lift consolidation without having large rocks protrude above the surface.
Padfoot drum machines expand the material range to include soils with more than 50 percent cohesive material and a greater percentage of fines. When the pad penetrates the top of the lift, it breaks the natural bonds between the particles of cohesive soil and achieves better compaction results. The pads are involuted to walk out of the lift without fluffing the soil and tapered to help them stay clean. The typical lift thickness for padded drum units on cohesive soil is in the 150- to 460-mm (6- to 18-in.) range.
Caterpillar has two pad shapes available: square faced pads and oval-faced pads. Square pads perform well on semi-cohesive soils and thinner lifts of less than 150 mm (6 in.). Square pads do a good job of sealing the surface.
Oval pads have less surface area than square pads, so they apply greater ground pressure than square pads. This allows the pad to penetrate deeper into the lift. Oval pads perform better on cohesive soils and thicker lifts of 150 to 460 mm (6 to 18 in.). Oval pads do not seal the surface as well as square pads.
Tamping Foot Compactors
Tamping foot compactors are high-speed, self-propelled, non-vibratory compactors. They usually have four padded steel wheels and are equipped with a dozer blade. Their pads are tapered with a rectangular face.
Tamping foot compactors compact from the bottom of the lift to the top. Because the pads are tapered, they can walk out of the lift without fluffing the soil. Therefore, the top of the lift is also being compacted and the surface is relatively smooth and sealed. Tamping foot compactors are capable of speeds in the 16-32 km/h (10-20 mph) range, but they typically operate in the 10-15 km/h (6 to 10 mph) range.
Generally, two to four cycles (4 to 6 machine passes) will achieve desired densities in 200- to 300-mm (8- to 12-in.) lifts although four cycles may be needed in poorly graded plastic silt or very fine clay. Tamping foot compactors are effective on all soils except clean sand.
Tamping foot compactors leave a fairly smooth, sealed surface so hauling units are able to maintain a high speed when traveling over the fill. Also, since dozer-equipped tamping compactors do both spreading and compacting, the contractor may be able to reduce the number of track-type spreaders.
Tamping foot compactors are best suited for large projects. They need long, uninterrupted passes to build up speed that generates high production. On lifts greater than 300-mm (12-in.) thick, tamping foot compactors are about two to three times more productive than single-drum vibratory compactors.
Sheepsfoot Compactors
Sheepsfoot compactors derived their name from the fact that early Roman road builders would herd sheep back and forth over base material until the road was compacted. The word “sheepsfoot” became a generic term to describe all types of padded drums. In reality, a sheepsfoot compactor is very different from a padded drum or tamping foot compactor.
A sheepsfoot pad is cylindrical, usually 200-mm (8 inches) long. The pad is circular and will range in diameter from 76 to 127 millimeters (3 to 5 inches). The pads on tamping foot or padded drums are tapered with an oval or rectangular shape. And the pad face is smaller than the base of the pad—that’s an important difference.
The pads on sheepsfoot drums penetrate through the top lift and actually compact the lift below. When a pad comes out of the soil, it kicks up or fluffs the material. The result is a loose layer of material on top. When more fill is spread, the top lift will be fluffed and the previous layer will be compacted. A sheepsfoot compactor truly compacts from the bottom up.
Using a sheepsfoot compactor has one definite benefit. Because the top lift of soil is always being fluffed, the process helps aerate and dry out wet clays and silts.
But the disadvantages of sheepsfoot compactors are numerous. The loose top-lift material can act as a sponge when it rains and slow the compaction process. The loose material also slows hauling units that deposit fill material, so haul cycle times are increased.
Plus, sheepsfoot compactors can work only at speeds from 6 to 10 km/h (4 to 6 mph), which cancels any benefit from impact and vibration. Pressure and manipulation are the only compactive forces exerted on the soil. Usually, 6-10 cycles (12-20 machine passes) are needed to reach target density on 200-mm (8-in.) lifts. Sheepsfoot compactors are no longer widely used.
Pneumatic Compactors
Pneumatic compactors are used on small-to-medium size soil compaction jobs, primarily on bladed, granular base materials. Often, they are used as a finishing compactor after a vibratory drum compactor completes compaction of the lift.
Pneumatic compactors are best suited for sealing the surface, special applications such as compaction of thin lifts, or special requirements dictated by the job.
The compactive forces (pressure and manipulation) generated by the rubber tires work from the top of the lift down to produce density. The amount of compactive force can be varied by altering the tire pressure (the normal method) or by changing the weight of the ballast (done less frequently).
The kneading action caused by the staggered tire pattern helps seal and smooth the surface. Pneumatic compactors can be used on soil and asphalt, an advantage that allows a roadbuilding contractor to use one compactor for multiple stages of construction.
This article and photos are courtesy of Cat Paving.