Thermal cracking – also known as low temperature cracking – in bituminous pavements appears as a series of transverse cracks that extend across the pavement surface in response to cold temperatures. Thermal crack intervals of 19 to 30 feet are typical, but may vary widely. The spacing of cracks often is regular over the length of a pavement.
Prolonged frigid temperatures can cause asphalt pavements to crack if the wrong performance graded (PG) asphalt binder is used for the climate, or if the binder has “aged” prematurely via excessive heat in the plant where it is made. That can lead to premature deterioration of a roadway and create the need for costly, congestion-causing repairs.
Highway agencies try to limit low temperature cracking by specifying Superpave performance-graded asphalt binders intended for their climate that have favorable properties at very low temperatures. However, aggregates that make up more than 90 percent (by weight) of a typical asphalt mix may respond in their own ways to low temperatures. Crude oils from which binder is produced will vary and result in liquid asphalt that interacts differently with aggregates.
In the design phase, the thermal cracking model included in the new Mechanistic-Empirical Pavement Design Guide (MEPDG) is an engineering tool that can be used to evaluate the potential for thermal cracking during design, says Ramon Bonaquist, Ph.D., P.E., Advanced Asphalt Technologies in Characterization of Wisconsin Mixture Low Temperature Properties for the AASHTO Mechanistic-Empirical Pavement Design Guide, published by the Wisconsin Highway Research Program of the Wisconsin DOT in December 2011.
This model performs a thermo-viscoelastic analysis of a constrained asphalt layer to compute stresses within the layer as a function of depth, Bonaquist says.
“Pavement temperatures as a function of depth and time for the thermal stress analysis are obtained from the environmental effects model,” Bonaquist says. “The computed thermal stresses are used in a linear fracture mechanics model to compute the propagation of a vertical surface crack through the asphalt layer. Finally, the crack spacing at the surface of the pavement is determined from an empirical model that relates the crack spacing observed in the pavement to the average crack depth calculate by the analysis.”
Getting the right mix design and PG binder notwithstanding, premature aging of liquid asphalt binder that has been damaged in the manufacture of hot mix asphalt (HMA) is receiving much of the blame for low temperature thermal cracking.
At a hot mix plant, when liquid asphalt is exposed to high heat in the aggregates dryer, lighter hydrocarbons can be stripped away, leaving a compromised binder that may perform as through it’s been part of a mix that’s been sitting in the blazing sun season after season, “aging” and becoming more brittle. Thus when the condition appears in a relatively new mix, the binder is said to have been prematurely aged.
Premature aging is avoidable. But preventing premature aging in asphalt binder is only one piece in solving the puzzle of building roads not to fail.
The addition of reclaimed asphalt pavement (RAP) and recycled asphalt shingles (RAS) into new asphalt mix design is on the increase, due to the high cost of petroleum, difficulties in procuring fresh reserves of quality virgin materials at economical distances from where they will be used and limited space in landfills.
Yet the use of RAP introduces design challenges because the residual asphalt binder in RAP becomes stiffer due to aging, and that stiffness is imparted to the mix. Stiffness is good because it bolsters a mix against rutting, but can be bad as it’s thought to contribute to thermal cracking.
Advance Testing for Thermal Cracking
Low-temperature thermal cracking is a major type of asphalt pavement failure, but analysis will help prevent it. said Sang-Soo Kim, associate professor of civil engineering, Russ College of Engineering and Technology, Ohio University, Athens, and member of the university’s Ohio Research Institute for Transportation and Environment, in the January-February 2013 issue of TR News of the Transportation Research Board.
In Kim’s article, The Asphalt Binder Cracking Device Test, the researcher says state DOTs allocate significant financial resources to repair or replace cracked pavements. “Properly grading asphalt binders for the expected climatic environment, however, can minimize premature pavement failure from thermal cracking,” Kim says.
Currently, two grading schemes are used to measure the low temperature performance of asphalt binders, he says, the bending beam rheometer (BBR) test, which measures creep properties, and the bending beam rheometer–direct tension (BBR-DT) test, which measures creep and failure properties.
“No standard test method determines the binder’s CTE [coefficient of thermal expansion]; this leaves some uncertainty when using current test methods to select the asphalt binder that will be most resistant to cracking at low temperatures,” Kim says. But now the asphalt binder cracking device (ABCD) test, developed under a National Cooperative Highway Research Program IDEA project, directly determines the low-temperature cracking potential of asphalt binders in field-like conditions, as the thermal contraction of the asphalt binder is restrained in order to generate thermal tensile stress to failure.
In the ABCD test, a binder sample is poured into a circular mold outside of a 2-inch diameter Invar ring. Invar is a steel alloy with a near-zero coefficient of thermal expansion, the author says. “The ring with the specimen is placed in a cooling chamber; as the temperature steadily decreases, the binder specimen contracts and compresses the ABCD ring,” he says. “Sensors inside the ABCD ring measure and record the temperatures and strains throughout the test. When the binder specimen cracks, the strain is relieved abruptly; the temperature at that moment is the ABCD cracking temperature.” The device has been further refined by the FHWA.
Kim’s device has shown how addition of polymer modifiers can fight low temperature thermal cracking, and that more modifier improves performance. “The ABCD test also measured the effects of polymer modification on the asphalt binder’s low temperature cracking more reliably than the BBR test,” he says. “The addition of polymer generally lowers the cracking temperature of asphalt pavements in cold environments. In tests on asphalt binders modified with styrene-butadiene-styrene (SBS), however, the BBR test indicated no visible lowering of the binder cracking temperature; in contrast, the ABCD test showed a gradual but distinct decrease of cracking temperature – that is, an improvement – with an increased concentration of polymer.”
Thus use of polymer modifiers to moderate potential thermal cracking due to premature aging of asphalt binder in the hot mix plant can work, but at a significant added cost. If the liquid asphalt binder can be incorporated in the mix at lower production temperatures, then premature aging of binder can be moderated as well. That has become one more reason behind the growing popularity of warm asphalt mixes.
RAP, RAS and Binder Stiffness
The residual asphalt binder in RAP will blend with virgin asphalt binder in almost any mix design, and the resulting properties of this blended asphalt binder must be understood, the Washington State DOT says. But the effect of RAP residual asphalt binder must be considered when using RAP in Superpave or any mix design, because RAP asphalt binder already is significantly aged.
“This aged binder is generally stiffer than virgin asphalt binder and thus will cause the resultant binder blend to become more viscous (stiffer),” WSDOT says. “This, in turn, will cause the HMA to be more viscous.”
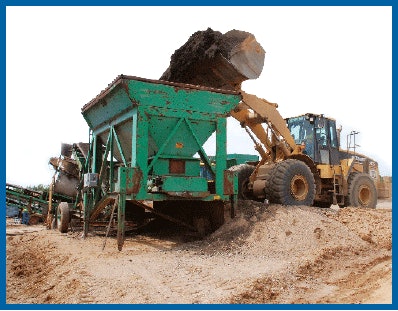
As a result, successful RAP mix designs incorporating RAP above 15 percent by weight should analyze the stiffness of the existing residual binder in the RAP, and compare it to the stiffness of the virgin liquid binder, along with the proportions of each in the final product.
Binders containing recycled asphalt roofing shingles (RAS) are even stiffer, note Fujie Zhou, Ph.D., P.E., Hongsheng Li, and Tom Scullion, P.E., Texas A&M Transportation Institute, and Robert Lee, P.E. and German Claros, Ph.D., P.E., Texas Department of Transportation in their 2013 Transportation Research Board paper, RAS Binder Characterization and Blending with Virgin Binders.
Shingles for asphalt recycling are sourced by suppliers that process the material into a crumb consistency, and can provide chemical analysis. RAS originates either as tear-off shingles (TOAS) from roofing projects, or as manufacture waste asphalt shingles (MWAS) from production.
“It is well known that the extracted/recovered shingle binders, regardless of MWAS or TOAS, are very stiff, and they are far stiffer than any PG 76-22 binder,” Zhous, Li, Scullion, Lee and Claros report. “It is important to determine the true grade of the RAS binder since it has significant influence on virgin binder selection and the maximum amount of RAS allowed in the asphalt mixes.”
Increasing the RAS binder amount will make the blended binder stiffer, with a positive effect on the mix’ high temperature property (or rutting resistance), but also a negative effect on its low temperature property (or cracking resistance), they say.
WMA Moderates Thermal Cracking
That warm mix asphalt is less susceptible to thermal cracking is becoming more and more evident.
In their 2013 Transportation Research Board paper, Fracture Resistance of Warm-Mix Asphalt Concretes at Low Temperatures, Sung-Jin Lee, Jiyong Park, Jun-Pyo Hong, and Kwang W. Kim, all of Kangwon National University, Republic of Korea, say WMA mixtures show higher fracture toughness than HMA at severely low temperatures.
Why? “WMA mixtures are much like HMA mixtures, but are produced at lower plant temperatures than conventional HMA mixtures,” they said in January. “Many studies investigated rut characteristics of WMA, but few studies have reported fracture characteristics, which is one of the major damage mechanisms of asphalt concrete in the pavement. Since asphalt becomes brittle at low temperatures, HMA concretes show brittle fracture at low temperatures.”
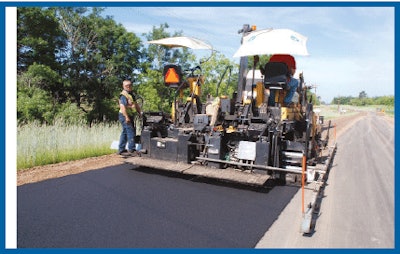
Fracture toughness is a property which describes the ability of a material containing a crack to resist fracture, and is one of the most important properties of any material in all design applications, they say. “The Kic or critical stress intensity factor is a quantitative way of expressing a material’s resistance to brittle fracture when a crack is present,” they write. “If a material has a large value of Kic, it will probably undergo ductile fractures and will have better resistance against deformation under large stresses before cracking. A brittle fracture is characteristic of materials with a low Kic value. Therefore, a large value of Kic is desirable for asphalt pavement material.”
Many studies have shown that HMA concrete failed catastrophically from brittle fractures at low temperatures, they say, which is the very definition of thermal cracking. “The behavior of a WMA concrete is in question under low temperatures, at which the WMA may also be in a brittle state,” they say. “Due to incomplete aggregate drying at the time of manufacturing, WMA concrete might be more vulnerable to fractures. On the other hand, WMA would be stronger against fractures than HMA due to the lower level of binder aging during processing, because of the lower short-term aging temperatures.”
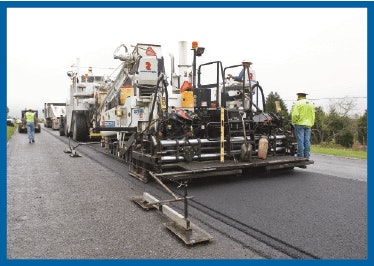
According to the critical stress intensity factor (Kic) analyses in this study, WMA concretes were found to have better Kic than HMA concretes, in most cases. “This means that the WMA concretes used in this study have stronger resistance to fracture than HMA concretes at the examined low temperature range,” they write. “One of the reasons probably acceptable to asphalt engineers is that due to a lower level of aggregate heating during production, it results in less short-term aging. The asphalt “aged”by hot aggregate would have to be much more brittle at low temperatures.
The researchers conclude:
• All mixtures showed critical stress intensity factor (Kic) increase by temperature decrease, making a peak at minus-15 or minus-20 degrees C [5 to -4 degrees F], then decreased with further lowering of temperatures. This kind of phenomenon, explained as the effect of differential thermal contraction damage in HMA mixtures, was also observed in WMA mixtures.
• The critical stress intensity factor values of WMA mixtures were observed to be higher than those of HMA mixtures, and in most cases at all temperatures evaluated in this study. Particularly after being subjected to DTC damage at minus-15 and/or minus-20 degrees C, most of the WMA mixtures showed higher critical stress intensity factor than HMA mixes at severely low temperatures.
• Therefore, it was concluded that the WMA mixtures used in this study had stronger resistance to brittle fractures than HMA mixtures when prepared with the same low temperature PG binders. The WMA mixtures were not more susceptible to DTC damage at low temperatures than HMA, even though they were produced at a relatively lower aggregate-heating temperature.
In Minnesota, Crow Wing County used a warm-mix asphalt additive – Evotherm from MWV Asphalt Innovations – to see if it could get from a lower-cost PG 58-28 binder the same cold-weather performance of the more expensive polymer-modified PG 58-34 binder specified in Minnesota for newly constructed low-volume bituminous roadways. One of its mixes used 30 percent RAP.
It also hoped to use the WMA additive to improve binder durability by reducing the premature aging to binder caused by exposure to the scorching heat of the asphalt plant burner.
“One of the hoped-for benefits of warm mix asphalt is greater durability over time,” says Wayne Dosh, senior engineering technician, Crow Wing County Highway Department. “One of the issues we struggle with in Minnesota is thermal cracking. It’s usually the biggest killer of our roads. One of the ways to get around it is by using softer grades of binder. The performance-grade binders used are based on our ambient temperature extremes, and with that kind of spread, that usually implies polymer modified asphalt. By using a warm mix additive, we hope to be able to get the same performance with a non-modified oil as with a modified.
“One of the benefits of warm mix over hot mix is that in the hot mix plant, the heat contributes to premature or artificial aging of the binder, which breaks down the oils,” Dosh says.
“This gets even worse as the mix ages in-place over time. One of the benefits we’re hoping from the warm-mix additive for is for us to be able to use cheaper binder – PG 58-28, that doesn’t require a polymer modifier – with the added benefit of less premature aging in addition to less thermal cracking.”