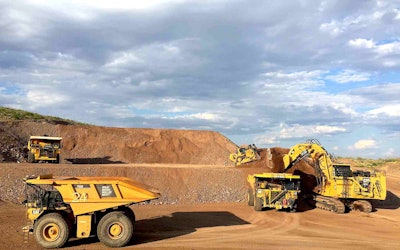
With 100 autonomous haul trucks expected to be working in mines across the world by the end of this year, Caterpillar is emphasizing its brand agnostic mining technology platform, part of its efforts to embed itself deep into a mine’s operation.
“Autonomy is no longer an experiment,” said Denise Johnson, Caterpillar Resource Industries group president at a Cat investor meeting held concurrently with the mining press conference. “We’re seeing increasing pull from customers, and we’re currently tracking 100-plus opportunities. We want to move fast in the space; our competition is coming from both traditional and nontraditional players.”
Cat says its current autonomous fleet includes 56 Cat 793F trucks that have achieved 20 percent greater production than manned trucks working in the same mining complex. These 56 trucks interact with more than 150 manned vehicles – graders, loaders, water carts, light vehicles and dozers – managed through the Cat MineStar System. In 4.5 years of operation, Cat says its autonomous trucks have hauled 400-plus million metric tons of material with greater than 99.95 percent system availability, all without a lost time injury. And because there are no shift changes, breaks or lunches, the trucks put in an average of 2.5 hours more work a day more than manned vehicles.
Tech partnerships
Cat’s brand agnostic approach deals with current mine realities: most mines have mixed fleets, partially caused by consolidation in the industry. As the mining industry starts to recover from the commodity price downturn, mines are beginning to use existing truck inventory, which can be a variety of brands, requiring a retrofit solution.
Key to this retrofit effort will be the partnerships it has formed with technical and financial companies, partnerships that in some cases have been long standing. “You don’t see all our suppliers on the iron side, but you will on the tech side,” says Sean McGinnis, product manager for Cat Mining Technology.
For example, Cat has been working with Torc Robotics for 10 years, a relationship that began when both companies were involved in the Defense Advance Research Projects Agency, or DARPA, autonomous vehicle Grand Challenge. Torc has since worked with Cat to develop Cat’s RemoteTask skid steer remote control system, introduced in 2015. And now Cat has partnered with Torc to develop a system where the Cat autonomous haul truck system can operate a Komatsu 930E haul truck, a product it plans to have on the market in the first quarter of 2019.
“Obviously the systems change when you go from one vehicle to another,” says Michael Fleming, CEO of Torc, based out of Blacksburg, Virginia. “With the 930E project, we were able to bring in experienced engineers that understand autonomy and what the trade-offs are, and then work with Cat’s expertise to create a product that works well. This is very complex technology; there are a lot of moving parts.”
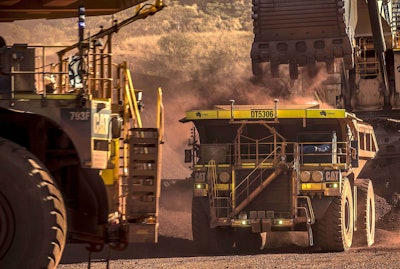
Fleming says mining is benefitting from Torc’s research in two other areas of concentration for the company: automobiles and defense. “Today, the automotive autonomous sector is very hot, and it will change our lives in ways that we don’t fully comprehend right now.”
Other partners in the mine technology space include IT-network giant Cisco, tasked with getting the data off the equipment and into the office, says Craig Watkins, Cat Mining Technology sales support. “It’s important that every wireless network component works, and as we go into LTE telecommunications networks, we stay ahead of the curve,” he says. “Any hiccups in communication can have a significant impact on a mine’s productivity. Now it’s not about building redundancy into a system, but understanding when things are about to degrade so you never get to the point of interrupted data.”
Caterpillar’s long-standing telematics partner Trimble is also in the mix. “Mining has always been a 3D environment and that 3D capability hasn’t been there,” says Nathan Pugh, Trimble’s director of mining. “Our challenge was to put in a visual intelligence layer, so you can get your point across different organizations.”
Cat has also made a strategic investment in Alight Solutions, which looks at financial forecasting and scenario analytics. One of Alight’s tasks is to take the MineStar data from a mine, compare it with Caterpillar’s benchmarking data from all mines and feed it into Alight’s forecasting and analytics system, says Michele McGovern, Alight CEO. For mines already operating, this can identify utilization and availability improvements, such as ways to optimally reconfigure haul roads. This analysis can also offer a “financial blueprint” for mines being developed, says McGovern.
Cat also has its eye toward maximizing scalability, bringing the large mine products and services into smaller operations, including quarries. “Our NextGen Minestar will be introduced in 2018 and will offer toe-in-the-water technologies, making it more accessible to quarry operations and smaller mine sites,” says Dan Hellige, Cat Mining Technology sales manager. “We want to create a broader and deeper base of actionable knowledge that can be shared throughout an organization.”
This scalability also applies to different machine types. Today, Cat’s Command for Hauling offers a fully autonomous truck solution. With drills, Cat is taking a stair-step approach, with a terrain guidance solution now, with plans to offer a semi-autonomous and then fully autonomous systems in the future. There, too, Cat is working on retrofit products, specifically for the P&H 320 XPC, which will go into testing this year, and the P&H 120A, piloting in the first quarter of next year. Dozers can now be remotely controlled and feature auto blade control and carry; semi-autonomous features will come later.
Technology not the hard part
The most significant challenges that remain as the industry takes steps toward autonomy are with people and processes, rather than technology. “Making a truck drive safely from point A to point B is not the hard part, but rather it’s the change management needed to make it work on a mine site,” Hellige maintains.
But part of that change has already taken place, reports Caterpillar. “Right now there’s a pull from our mining customers,” says Cat’s Watkins. “From the start of the year, mines have suddenly started talking to us about doing more than an iron transaction.”
During the investor meeting, one analyst asked Group President Johnson if the increased productivity of unmanned trucks wouldn’t mean fewer truck sales. Yes, she said, “but we we’re also looking at the alternative, which would be to allow someone else to have this space. This is helping to improve the productivity of the entire site, not just a certain piece of equipment. That’s where the real value proposition comes in, when we get to the trusted advisor position.”