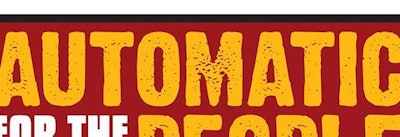
That’s what makes trucking today so interesting: It is going through several revolutions and evolutions at the moment. The advent of automatic and automated transmissions in heavy-duty commercial vehicles is one such example. In many ways, the explosion in popularity of these units over the past decade is an offshoot of the rapid evolution being seen in onboard vehicle computers.
Automatic transmissions are nothing new. They’ve been around in automotive applications in one form or the other since the 1940s. But adapting them for use in trucking proved to be difficult for a variety of reasons – not the least of which was the inability of mechanical engines and transmissions to “talk” to one another and insure optimal vehicle performance in the bewildering array of applications, road conditions and cargo/payload configurations North American heavy and medium-duty trucks see on a daily basis.
As a consequence, early attempts to develop and introduce were met with less than acceptable results. There were durability issues. But most complaints tended to focus on performance issues: Before the advent of today’s powerful and compact electronic control modules, early transmissions had a hard time figuring out what drivers wanted. Complaints concerning frequent, uneven shifts while accelerating were common, as were problems with “searching,” when transmissions would struggle in hilly terrain to find – and stick with – an optimal gear. Other problems along those lines emerged at low speeds.
“I sold some early AMTs to fleets back in the late 1980s,” says David McKenna, director of powertrain sales for Mack Truck. “There were a lot of problems with those units. And today, when I call on a fleet to talk about our new mDrive, sometimes the biggest problem I have is not getting thrown out of the office when I mention the term “automated transmission!’”
Other issues come into play today as well, McKenna notes. “Our customers want somebody else to try stuff out and see if it works. And, frankly, they’ve had a lot of new, unwanted technologies to deal with over the past several years on the emissions front. So in some ways, they’re a bit worn out and digesting things slowly.”
Still, it looks like time is running out for the tried and true manual gearbox.
Dry clutches and torque convertors
Although in the interest of brevity, I am using the term “automatic” to refer to all non-manual gearboxes, it’s important to note that there are actually two different types of automatic transmissions available for heavy-duty trucks today: Automated manual transmission and automatic transmissions.
Both types of transmissions are two-pedal designs. And most drivers would be hard-pressed to tell much of a difference between them.
The basic difference is that automated manuals are manual gearboxes with all the clutch actuation and gearshifts handled by electronically-controlled systems. True automatic transmissions feature planetary gearing with disc packs for clutches and with torque converters. “In this context, an automatic for a Class 8 truck is usually fully automatic, like a typical car transmission, with planetary gearing with several multi-disc packs for clutches,” says Ed Saxman, product marketing manager with Volvo Trucks North America.
“These transmissions have a torque converter to enable powershifts of the planetary epicyclic gearing units that provide the various gear ratios. An automated manual transmission uses the gearbox of a manual transmission and shifts it by computer, using a computer-operated single large diameter disc clutch otherwise similar to a manual clutch.”
“The Allison Automatic transmission has Continuous Power Technology, which means it never interrupts torque and power to the wheels,” explains Steve Spurlin, executive director, international application engineering and vehicle integration for Allison Transmission. “It also uses a torque converter as the starting device. An automated manual has incorporated electronic controls with basic manual transmission architecture to facilitate automated shifting of gears and of the input clutch starting device. Both the automated manual and the basic manual interrupt power and torque every time a shift is made whether automated or manually.”
According to Steve Rutherford, powertrain marketing manager, Caterpillar OEM Solutions Group, the advantages of a pure automatic design are a perfect fit for the company’s vocational truck line – although he points out that both types of transmissions work well in specific applications. “Both types of transmissions have two pedals and a shift pad instead of a gearshift lever,” he notes. “It took a lot of work to perfect automated manuals to engage a dry clutch and generate well-synchronized shifts. What they’ve done with those products is amazing.”
But in construction applications, Rutherford says, with lots of starts and stops in muddy terrain with high rolling resistance, or having smooth, controllable startup power in front of a paver, an automatic transmission is the better choice in Caterpillar’s estimation. “You just cannot beat a torque converter in those applications when it comes to maintaining 100 percent boost engine power up and down through the gears,” he says.
“Additionally, there’s not a dry clutch to be abused or overheat because an automatic is 100-percent fluid drive power. So that’s where we see the advantages of a torque convertor automatic. However, in a steady-state cruise application in pure highway mode, you simply cannot beat an automated manual: They really shine in those applications.”
The case for automatics
Despite their reputation as slow to change, it appears users are gravitating toward automatic transmissions in surprisingly high numbers. McKenna, for example, says the mDrive take rate in Pinnacle tractors is currently in the neighborhood of 38 percent, which aligns with other OEMs. In some medium duty applications, AMTs are now spec’d in over half of new trucks sold. Likewise, Saxman says that well over 50 percent of all new Volvos sold this year have been spec’d with the company’s iShift AMT.
There are several reasons for this significant shift. Shane Groner is manager of product development, NAFTA, for Eaton. He says currently the company’s UltraShift Plus AMT is enjoying a 25 percent take rate in heavy-duty trucking applications – with on-highway applications logging in around 15 percent. “There are still a lot of highly experienced drivers out there that can get the most out of manual transmission,” Groner says. “And those gearboxes are essentially bulletproof. So if you’re blessed with an abundance of experienced drivers and upfront costs are still your primary expense driver, then it’s hard to argue with manual transmissions.”
The appeal of automatics can go far beyond driver preferences, with safety and fuel economy topping the list. “Automatics allow less skilled (novice) drivers to be productive,” says Steve Spurlin, executive director, international application engineering and vehicle integration for Allison Transmission. “They are also a large help with safety because the drivers can stay focused on the road or the task at hand instead of shifting gears. Additionally, drivers do not get as fatigued with an automatic as they do with a manual or AMT since they do not have to shift gears all of the time.”
“The way you spec a drivetrain is changing and automatic transmissions are a key part of that formula,” says Brad Williamson, powertrain marketing manager for Daimler Trucks North America. “The industry at large is now spec’ing lower gear ratios with direct drive powertrains becoming more common.”
At the same time, Williamson says, the concept of “downspeeding” – or operating a diesel at lower rpms while at cruise speeds are being driven by the push for better fuel economy. “An automatic transmission can do these things better than all but the best drivers out there. Because information is key: If you designed both the engine and the transmission, then they can ‘talk’ to one another and share critical information. And the transmission can manage all this information and deliver the best performance possible given all those criteria. A driver just can’t do that consistently.”
Williamson’s point is important because it addresses the latest development in the evolution of automatics in heavy-duty trucking: complete powertrain integration. To date, Volvo, Mack, Daimler and Eaton (with a just-announced partnership with Cummins) have all developed highly integrated powertrains that share unprecedented levels of proprietary information between the engine and transmission to consistently deliver optimal fuel economy at all times.
“It all boils down to the electronics,” McKenna argues. “When you have Vendor A supplying the engine and Vendor B supplying a transmission, rarely do those two components share 100 percent of their information 100 percent of the time. Typically, the transmission in those instances ends up making decisions with about 75 percent of the data it needs to make an optimal shift. “
Eaton’s Groner says that a fully-integrated drivetrain can boost fuel economy from 3 to 6 percent above what a vehicle with a non-integrated drivetrain achieves. “And that’s with an EPA 2013 engine,” he adds. “Our testing shows those numbers are even higher on EPA ’10 engines.” EW